A clear and organized warehouse structure is essential for running efficient operations within a Warehouse Management System (WMS). The hierarchical design of a warehouse structure helps in effectively managing inventory, improving stock visibility, and streamlining processes. This guide explains the different levels of a WMS warehouse structure using tables for clarity, followed by detailed explanations.
Overview of Warehouse Structure in WM
A warehouse structure in WMS is hierarchical, starting from the warehouse number and breaking down into more granular elements like storage types, storage sections, storage bins, and quants.
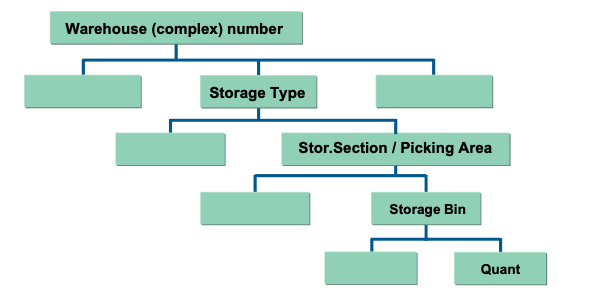
Warehouse Hierarchical Elements
Hierarchy Level | Description |
---|---|
Warehouse Number | Represents the entire warehouse complex. |
Storage Type | Functional subdivisions of the warehouse (e.g., high-rack storage, picking). |
Storage Section | Logical groupings within a storage type for better organization. |
Storage Bin | Smallest physical storage locations for inventory. |
Quant | Represents the specific quantity of material stored in a bin. |
Each of these levels plays a unique role in ensuring smooth warehouse operations. Let’s dive deeper into each component.
1. Warehouse Number
The warehouse number is the highest level in the warehouse structure and represents the entire warehouse complex. All storage activities, types, and processes are grouped under this identifier.
Feature | Description |
---|---|
Central Identifier | Uniquely identifies the warehouse complex. |
Integration | Connects WMS to Inventory Management (IM) at the storage location level. |
Example | Warehouse Number 001 represents a warehouse with high-rack, bulk, and picking areas. |
Explanation:
The warehouse number is the central hub of your WMS setup. It integrates seamlessly with your plant’s Inventory Management (IM) system, enabling smooth communication between different stock levels.
For example: if Plant 0001 uses WMS, it assigns storage locations like 0088 to warehouse number 001.
2. Storage Types
Within a warehouse number, storage types divide the warehouse into functional areas. Each storage type is designed for a specific purpose.
Storage Type | Purpose |
---|---|
High-Rack Storage | Stores palletized goods in racks. |
Bulk Storage | Stores large, heavy items directly on the floor in rows. |
Picking Area | Dedicated area for frequently accessed items for order fulfillment. |
Return Area | Handles customer returns for reprocessing or quality checks. |
Explanation:
Storage types simplify warehouse management by creating logical groupings for inventory.
Example:- High-rack storage is ideal for long-term storage, while picking areas ensure quick access to fast-moving items. Storage types also allow businesses to define specific rules for how goods are stored, retrieved, or moved.
3. Storage Sections / Picking Areas
Each storage type is further divided into storage sections or picking areas, which create more specific groupings.
Feature | Purpose |
---|---|
Storage Sections | Groups similar storage bins (e.g., heavy items vs. fragile items). |
Picking Areas | Organizes bins for faster and more efficient order fulfillment. |
Explanation:
Storage sections allow businesses to categorize inventory based on characteristics such as weight, fragility, or handling requirements. Picking areas are optimized for quick access during order processing. For example, in a high-rack storage type, a section could store fragile items on lower shelves and heavier items higher up.
4. Storage Bins
A storage bin is the smallest unit in a warehouse where materials are physically stored. Every storage bin is uniquely identified for easy tracking.
Feature | Description |
---|---|
Bin Identification | Each bin has a unique ID (e.g., Rack-A1-B2). |
Granular Tracking | Allows precise tracking of inventory in each bin. |
Multi-Material | Bins can store one or more types of materials. |
Explanation:
Storage bins provide the exact location of materials within a storage section. For instance, a high-rack storage area could have bins labeled HR01-01
, HR01-02
, and so on. Using technology like barcodes or RFID tags, bins can be tracked with precision, reducing errors and retrieval times.
5. Quant
A quant is the smallest unit of inventory tracked in a WMS. It represents a specific quantity of material stored in a bin.
Feature | Description |
---|---|
Definition | Quantity of a specific material stored in a specific bin. |
Batch Control | Differentiates between batches or production dates of the same material. |
Explanation:
Quants enable the system to distinguish between batches, expiry dates, or stock movements for the same material stored in a bin. For example, a bin might hold two quants of Product A—one batch produced in January and another in February.
How These Levels Work Together
Let’s consider an example:
Hierarchy Level | Example Value |
---|---|
Warehouse Number | 001 |
Storage Type | 001 (High-Rack Storage) |
Storage Section | 001 (Fragile Items) |
Storage Bin | HR01-01 |
Quant | 100 units of Product A, Batch #123 |
This hierarchy ensures that stock is organized, tracked, and retrieved seamlessly. When a retrieval request is made, the system pinpoints the exact location (e.g., Bin HR01-01) and retrieves the specified quant (e.g., 100 units of Product A, Batch #123).
Benefits of a WMS Warehouse Structure
Benefit | Description |
---|---|
Granular Tracking | Tracks inventory down to the bin and quant levels. |
Improved Efficiency | Streamlines stock movements, retrievals, and replenishments. |
Better Visibility | Provides real-time insights into stock levels and locations. |
Integration | Works seamlessly with IM and other ERP modules like Sales and QM. |
Scalability | Adapts to growing warehouses with minimal reconfiguration. |
Conclusion
The warehouse structure in Warehouse Management is a robust hierarchy that ensures every item in the warehouse is tracked with precision. By organizing inventory into warehouse numbers, storage types, sections, bins, and quants, businesses can optimize workflows, improve visibility, and reduce errors.