Implementing a Warehouse Management System (WMS) revolutionizes how warehouses are structured and managed, offering granular control, real-time visibility, and optimized operations. This guide explains how WMS integrates with plant storage locations, organizes warehouse types, and manages inventory at the storage bin level, enhancing overall warehouse efficiency.
Understanding Warehouse Structure With WMS
A warehouse structure with WMS involves defining warehouse complexes and organizing them into storage types such as:
- High-rack storage
- Block storage
- Picking areas
These storage types are grouped under a warehouse number, which acts as a central identifier for managing all activities.
Key Features of a WMS Warehouse Structure
Feature | Description |
---|---|
Warehouse Number | Represents a collection of storage types within a warehouse complex. |
Storage Types | Subdivisions of a warehouse (e.g., high-rack storage, bulk storage). |
Storage Bins | Smallest physical locations where stock is stored and managed at a granular level. |
Integration with IM | Links stock levels at the storage location level with storage bin details. |
How to Structure a Warehouse With WMS
1. Defining Warehouse Numbers
A warehouse number groups storage types within a plant or across multiple plants.
- Each warehouse number is assigned to a storage location in Inventory Management (IM).
- Example:
- Plant 0001: Storage location 0088 → Warehouse number 001.
- Plant 0002: Storage location 0077 → Warehouse number 002.
2. Organizing Storage Types
Within each warehouse number, storage types are defined to represent distinct functional areas of the warehouse.
Example Storage Types in a Warehouse Complex
Warehouse Number | Storage Types | Purpose |
---|---|---|
001 | 001 (High-Rack Storage) | For palletized items. |
002 (Bulk Storage) | For large or heavy goods. | |
003 (Picking Area) | For frequently accessed items. | |
002 | 001 (High-Rack Storage) | Shared functionality. |
002 (Bulk Storage) | Shared functionality. | |
004, 005 (Additional Functional Areas) | Specialized purposes. |
3. Assigning Storage Bins
In WMS, storage bins are defined for each storage type. These bins represent the smallest physical locations for stock management.
Key Points:
- Each bin is tied to specific materials, enabling detailed tracking.
- Stock is managed at the storage bin level in WMS, while Inventory Management (IM) handles stock at the storage location level.
Pro Tip: Use barcode labels or RFID tags for efficient bin-level tracking.
4. Linking IM and WMS
To integrate Inventory Management (IM) with WMS:
- Assign a warehouse number to the relevant storage location in IM.
- This ensures seamless data flow between storage location stock totals in IM and bin-level details in WMS.
Example Configuration Path:
- Navigate to:
Enterprise Structure → Assignment → Logistics Execution → Assign Warehouse Number to Plant / Storage Location
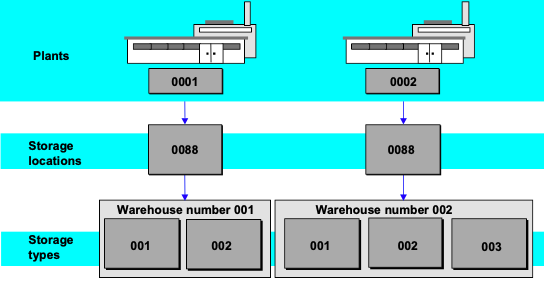
Managing Multiple Plants and Storage Locations in WMS
WMS offers flexibility to handle multiple plants or storage locations within the same warehouse number:
Scenarios
- Single Plant, Multiple Storage Locations:
- Example: Plant 0001 manages both high-rack and bulk storage (locations 0088 and 0077) under warehouse number 001.
- Multiple Plants, Shared Warehouse:
- Example: Plants 0001 and 0002 share the same warehouse number (001) for their storage locations.
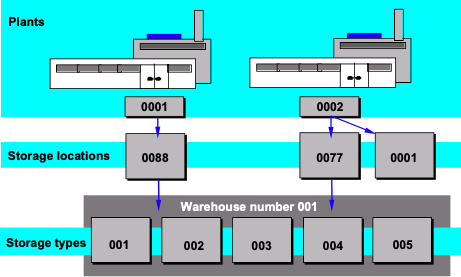
Benefits of a Warehouse Structure With WMS
Benefit | Description |
---|---|
Granular Stock Management | Tracks inventory at the storage bin level for precise control. |
Integrated Processes | Links warehouse activities with Quality Management (QM), Product Planning (PP), and Sales and Distribution (SD). |
Real-Time Inventory Visibility | Provides instant updates on stock location and quantities. |
Optimized Resource Usage | Enables efficient use of space and faster picking through system automation. |
Comparison: Without WMS vs. With WMS
Feature | Without WMS | With WMS |
---|---|---|
Storage Levels | Managed at storage location level | Managed at storage bin level. |
Random Storage | Not supported | Fully supported. |
Stock Tracking | Total quantities | Detailed per-bin tracking. |
Automation | Minimal | Advanced automation available. |
Scalability | Limited | Highly scalable for large operations. |
When to Use a WMS Warehouse Structure
A WMS structure is ideal if:
- You require bin-level tracking for high SKU variability.
- Your warehouse operations involve complex workflows, such as cross-docking or dynamic storage.
- You need integration with other processes, including QM, PP, or SD.
Conclusion
A warehouse structure with WMS provides unparalleled control and efficiency by organizing warehouses into storage types, managing inventory at the storage bin level, and integrating seamlessly with Inventory Management (IM). While it requires a more sophisticated setup, the benefits—such as real-time tracking, automation, and scalability—make it an indispensable tool for modern warehouse operations.