Overview of SAP Production Planning
SAP Production Planning (PP) is a crucial component of the SAP ERP system that helps businesses plan and manage their production processes effectively. It integrates with other SAP modules like Materials Management (MM), Sales and Distribution (SD), and Controlling (CO), providing a seamless flow of information that helps maintain efficient production lines and inventory management.
The primary role of SAP PP is to ensure that production runs smoothly and materials are available when needed, enabling businesses to meet their manufacturing demands efficiently. This includes activities such as Material Requirements Planning (MRP), Bill of Materials (BOM) Management, and Production Orders. SAP PP is used by manufacturers across different industries, from electronics to automotive, due to its versatility and powerful features.
Key Features of SAP PP
SAP PP offers a range of features that help streamline production:
- Material Requirements Planning (MRP): MRP ensures material availability for production and helps in efficient inventory management.
- Bill of Materials (BOM): A structured list of components required to produce a finished product.
- Production Orders: Helps in creating and managing production orders, detailing the quantity of products to be produced and the operations required.
- Routing: Defines the sequence of operations needed to manufacture a product, detailing the work centers and machine times required.
- Work Centers: Locations within production where specific operations take place, such as machines or production lines.
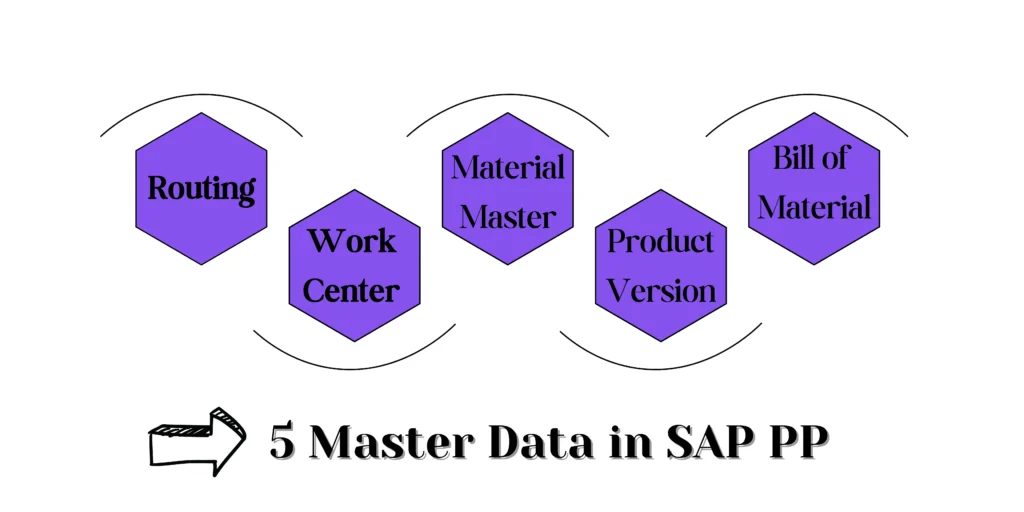
These features enable companies to have better control and visibility over their production processes, helping them make informed decisions about manufacturing schedules, materials, and costs.
Basic Navigation in SAP PP
For beginners, navigating SAP can be overwhelming. Here are some basics that will help you get started with SAP PP:
- SAP Easy Access Screen: This is the default landing page where you can access different functions and Tcodes (Transaction Codes) in SAP. You can use the navigation bar to find specific functions related to Production Planning.
- Transaction Codes (Tcodes): Tcodes are shortcuts used in SAP to perform specific tasks. In SAP PP, some common Tcodes are:
- MD01: Run MRP for materials.
- CO01: Create a production order.
- CS01: Create a Bill of Materials (BOM).
Introduction to Tcodes in SAP PP
Transaction Codes (Tcodes) are an integral part of working with SAP PP, allowing users to quickly access functions and execute tasks without navigating through the menus. Here are some commonly used Tcodes in SAP PP:
- CS01/CS02/CS03: To create, modify, and display a Bill of Materials (BOM).
- CR01/CR02/CR03: To create, change, and display Work Centers.
- CA01/CA02/CA03: For creating, modifying, and displaying Routing.
- CO01/CO02/CO03: For managing Production Orders.
These Tcodes help to simplify workflows and make the process faster by directly taking users to the desired function.
Integration with Other SAP Modules
SAP PP does not work in isolation; it integrates deeply with other SAP modules to facilitate the seamless flow of data and ensure effective planning and execution. Some key integrations include:
- Materials Management (MM): SAP PP uses material data from MM to plan production activities. MM helps with inventory management, procurement, and stock levels, which are essential for effective production planning.
- Sales and Distribution (SD): Sales orders from SAP SD influence production planning in SAP PP. For example, customer orders may trigger MRP runs to ensure enough materials are available to fulfill demand.
- Controlling (CO): Costing data from SAP CO is used to determine the cost of production, helping businesses track profitability and make cost-effective decisions.
Benefits of SAP Production Planning
- Optimized Production Scheduling: SAP PP helps businesses plan production schedules to avoid downtime and ensure the availability of necessary resources.
- Improved Inventory Management: With effective MRP, companies can ensure they have the right materials in the right quantity, minimizing excess inventory and reducing costs.
- Cost Efficiency: By linking production orders to the Controlling (CO) module, SAP PP provides insights into production costs, helping in budgeting and cost control.
Conclusion
SAP Production Planning is an essential part of managing a manufacturing process effectively. By providing tools for planning, managing resources, and integrating with other key modules, SAP PP helps manufacturers maintain a streamlined production flow, ensuring that products are produced on time and within budget.
Whether you are just starting out or are an advanced user, understanding the basics of SAP PP and its role in the broader SAP ecosystem will help you make the most of this powerful module.