Introduction to MRP in SAP PP
Material Requirements Planning (MRP) is a vital component in manufacturing and production industries. It is a systematic approach used to calculate the materials and components needed to manufacture a product. MRP tightly integrates various modules within SAP, specifically Materials Management (MM), Sales and Distribution (SD), and Production Planning (PP). This integration ensures that material planning aligns with both sales orders and production schedules.
Importance of MRP in Ensuring Material Availability
- Efficient Inventory Management: MRP helps maintain optimal inventory levels, preventing overstocking or stockouts of finished goods, raw materials, consumables, and more.
- Production Planning: Aligns production schedules with customer demand and plant requirements, ensuring timely fulfillment of orders.
- Cost Reduction: Optimizes inventory levels and reduces waste, contributing to cost savings.
- Improved Customer Service: Ensures materials are available when needed, enhancing customer satisfaction by meeting delivery commitments.
- Resource Optimization: Enables efficient use of materials, labor, and equipment through better scheduling and planning.
Understanding Material Requirements
In both manufacturing and distribution companies, daily material requirements are crucial to ensure that customer deliveries are made on time. When a customer places an order, it’s essential to confirm that the required materials are available by the customer’s desired delivery date. Fulfilling this commitment strengthens customer relationships and enhances the company’s reputation.
How MRP Works
MRP operates based on the total demand for materials, which can come from:
- Open Sales Orders: Existing customer orders that have been placed but not yet fulfilled.
- Planned Independent Requirements (PIRs): Forecasted demands determined either manually or through forecasting modules like SAP’s APO (Advanced Planning and Optimization).
Calculating Material Requirements
The MRP process involves several key steps:
- Determine Total Demand
- Example: Suppose the total demand for a material is 1,000 units in a month.
- Sources of Demand:
- Open sales orders.
- Planned independent requirements from forecasting.
- Assess Stock Availability
- Check current stock levels in the system.
- Example: There are 500 units already available in stock.
- Consider Open Purchase Requisitions (PRs) and Purchase Orders (POs)
- Identify any existing PRs or POs expected to deliver materials soon.
- These are considered planned receipts.
- Calculate Net Requirements
- Formula:
Net Requirements = Total Demand - Available Stock - Planned Receipts
- Example:
Net Requirements = 1,000 units (Total Demand) - 500 units (Available Stock) - 200 units (Planned Receipts) = 300 units
- Formula:
- Generate Procurement Proposals
- If there are shortages:
- For Finished Products: MRP creates Planned Orders that can be converted into Production Orders.
- For Raw Materials: MRP generates Purchase Requisitions that can be converted into Purchase Orders.
- If there are shortages:
Overall MRP Process
MRP ensures that material planning is proactive, accounting for all aspects of supply and demand. It’s one of SAP’s oldest and most essential functionalities, introduced over 25 years ago, and remains integral to efficient supply chain management.
MRP Processes
MRP Types
Different planning methods manage materials based on their characteristics and demand patterns. Below is a table summarizing the main MRP types:
Table: Summary of MRP Types
MRP Type | Description | Functionality | Usage |
---|---|---|---|
PD | MRP (Planning) | Calculates net requirements based on sales orders, planned demands, and stock levels. | Ideal for materials with dependent demand, typically components used in production of finished goods. |
VB | Manual Reorder Point Planning | Triggers procurement when stock levels fall below a predefined reorder point. | Suitable for materials with independent demand and relatively stable consumption patterns. |
VV | Forecast-Based Planning | Utilizes historical consumption data to forecast future requirements. | Applied to materials with variable demand where forecasting improves planning accuracy. |
PD with MRP Areas | MRP with Specific Areas | Allows planning at granular levels like storage locations or subcontractors. | Beneficial for detailed planning control across various locations or vendors. |
Choosing the Right MRP Type
Selecting the appropriate MRP type depends on factors like demand variability, lead times, and the criticality of materials. Proper selection ensures efficient material planning and inventory management.
MRP Run
An MRP run calculates material requirements and generates procurement proposals. In SAP, transaction codes MD01, MD04, and MMBE are commonly used for executing MRP runs, analyzing results, and checking stock availability.
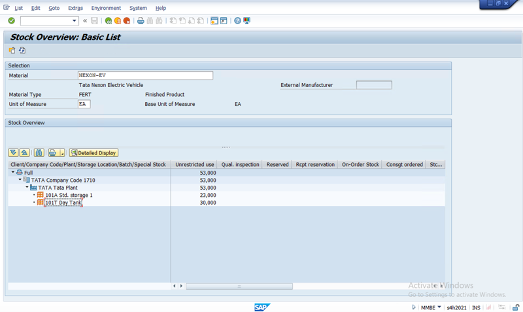
Executing MRP Using MD01
Step-by-Step Guide
Table: Steps to Execute MRP Run Using MD01
Step | Action | Details |
---|---|---|
1 | Access MD01 Transaction | Enter transaction code MD01 in the SAP command field and press Enter. |
2 | Enter Planning Scope | – Total Planning for Plant: Specify the plant for the MRP run.- Processing Key: Choose NEUPL, NETCH, or NETPL as required. |
3 | Define Planning Parameters | – Create Purchase Requisitions: Select if needed.- Scheduling: Choose between basic dates or lead-time scheduling.- MRP Control Parameters: Set planning mode and scheduling options. |
4 | Execute MRP Run | Click on the Execute button or press F8. |
5 | Review MRP Run Status | The system displays messages indicating success or any issues encountered. |
Analyzing Results Using MD04
Step-by-Step Guide
Table: Steps to Analyze MRP Results Using MD04
Step | Action | Details |
---|---|---|
1 | Access MD04 Transaction | Enter transaction code MD04 in the SAP command field and press Enter. |
2 | Enter Material and Plant | Input the Material Number and Plant to view the stock/requirements list. |
3 | Analyze Stock/Requirements List | – Available Stock: Check inventory levels.- Receipts and Issues: Review planned orders and requisitions.- Exception Messages: Note any alerts. |
4 | Drill Down for Details | Double-click on line items to view detailed information on dates, quantities, and sources of demand or supply. |
5 | Adjust Planning as Necessary | Make adjustments to procurement proposals or address exceptions based on analysis. |
Checking Stock Availability Using MMBE
MMBE is the transaction code used to check the stock availability of a material across different organizational levels.
Step-by-Step Guide
Table: Steps to Check Stock Availability Using MMBE
Step | Action | Details |
---|---|---|
1 | Access MMBE Transaction | Enter transaction code MMBE in the SAP command field and press Enter. |
2 | Enter Material Data | Input the Material Number and select the organizational levels (e.g., plant, storage location). |
3 | View Stock Overview | The system displays the stock quantities at various levels, including unrestricted, quality inspection, blocked stock, etc. |
4 | Analyze Stock Positions | Assess the availability of materials for planning and execution purposes. |
Tips for Effective Analysis
- Regular Monitoring: Frequently check stock levels to anticipate shortages or surpluses.
- Exception Management: Use exception messages in MD04 to address potential issues promptly.
- Collaboration: Coordinate with purchasing and production teams based on stock insights.
MRP Profiles
Configuration and Significance of MRP Profiles
What is an MRP Profile?
An MRP Profile in SAP is a set of pre-defined parameters assigned to materials to streamline and standardize MRP settings across similar items.
Benefits of Using MRP Profiles
- Standardization: Ensures consistent MRP parameters for groups of materials.
- Efficiency: Saves time by reducing repetitive data entry.
- Flexibility: Allows quick adjustments to planning parameters when needed.
- Error Reduction: Minimizes the risk of incorrect data entry for critical planning fields.
Configuring MRP Profiles
Step-by-Step Guide
Table: Steps to Configure an MRP Profile
Step | Action | Details |
---|---|---|
1 | Access MRP Profile Maintenance | Use transaction code MMD1 to create MRP profiles. |
2 | Create a New MRP Profile | Click on Create and enter a unique profile name and description. |
3 | Define MRP Parameters | – MRP Type: Set default (e.g., PD, VB).- Lot Sizing Procedure: Choose method.- Reorder Point: Set if applicable.- Safety Stock: Define levels.- Planning Time Fence: Establish period. |
4 | Set Default Values and Field Selection | Determine field statuses (mandatory, optional, display-only) and assign default values to reduce manual entry. |
5 | Save the MRP Profile | Review settings and save the profile. |
Assigning MRP Profiles to Materials
Table: Steps to Assign an MRP Profile to a Material
Step | Action | Details |
---|---|---|
1 | Access Material Master Record | Use transaction code MM01 (create) or MM02 (change). |
2 | Assign MRP Profile | On the MRP data screens, enter the MRP Profile you created; the system populates default values. |
3 | Review and Adjust as Needed | Verify default values for the material and make adjustments if necessary. |
4 | Save the Material Master Record | Save changes to apply the MRP profile to the material. |
Best Practices
- Group Similar Materials: Create profiles for materials with similar planning requirements.
- Regular Updates: Review and update MRP profiles periodically to reflect changes in planning strategies.
- Documentation: Maintain clear documentation of MRP profiles for training and consistency.
Conclusion
Understanding and effectively utilizing MRP and its components is crucial for efficient supply chain and production management. By mastering MRP types, executing MRP runs, analyzing results, and configuring MRP profiles, organizations can significantly improve their material planning processes, reduce costs, and enhance customer satisfaction.
Key Takeaways
- MRP ensures material availability by aligning procurement with production schedules and customer demands.
- Selecting the appropriate MRP type is essential for accurate and efficient planning.
- Executing and analyzing MRP runs helps in proactive inventory management and addresses potential shortages.
- MRP profiles streamline the planning process, promoting efficiency and consistency across materials.
- Stock Availability Checks: Regularly using transactions like MMBE ensures up-to-date information on material stocks.
Further Reading and Resources
- SAP Help Portal: Detailed documentation on MRP functionalities.
- APICS Certifications: Professional courses on production and inventory management.
- Industry Case Studies: Learn from real-world implementations of MRP systems.
For any questions or assistance with MRP processes, feel free to reach out to your system administrator or SAP support team.