Planning strategies in SAP PP define the approach to planning and manufacturing a material. They determine how materials are produced, whether based on forecasts (Make-to-Stock) or customer requirements (Make-to-Order). These strategies govern the interaction between sales and production, influencing how independent requirements are consumed by sales orders and how warehouse stock is utilized during the Material Requirements Planning (MRP) run.
Different Planned Strategies in SAP PP?
Planning strategies are categorized based on the production approach:
Planning Type | Description | Examples |
---|---|---|
Make-to-Stock (MTS) | Production is based on forecasts and inventory is used to fulfill customer orders. | Strategies 10, 40 |
Make-to-Order (MTO) | Production is triggered by customer orders and is unique to each sales order. | Strategies 20, 50 |
Assembly-to-Order (ATO) | Combines MTS and MTO; sub-assemblies are forecasted, and final assembly is done upon order receipt. | Strategies 81, 82 |
This table provides a clear differentiation between the types of planning strategies, aligning them with business scenarios. For instance, MTS works well for standard products, while MTO suits customized orders.
Make-to-Stock Strategies
In Make-to-Stock (MTS), production is initiated based on planned independent requirements (PIRs), and customer orders are fulfilled from inventory.
Strategy | Key Features |
---|---|
Strategy 10 | Pure MTS; customer orders don’t influence production plans. PIRs drive production, and stock is consumed during delivery. |
Strategy 40 | MTS with final assembly; customer orders consume PIRs, enabling dynamic planning adjustments. |
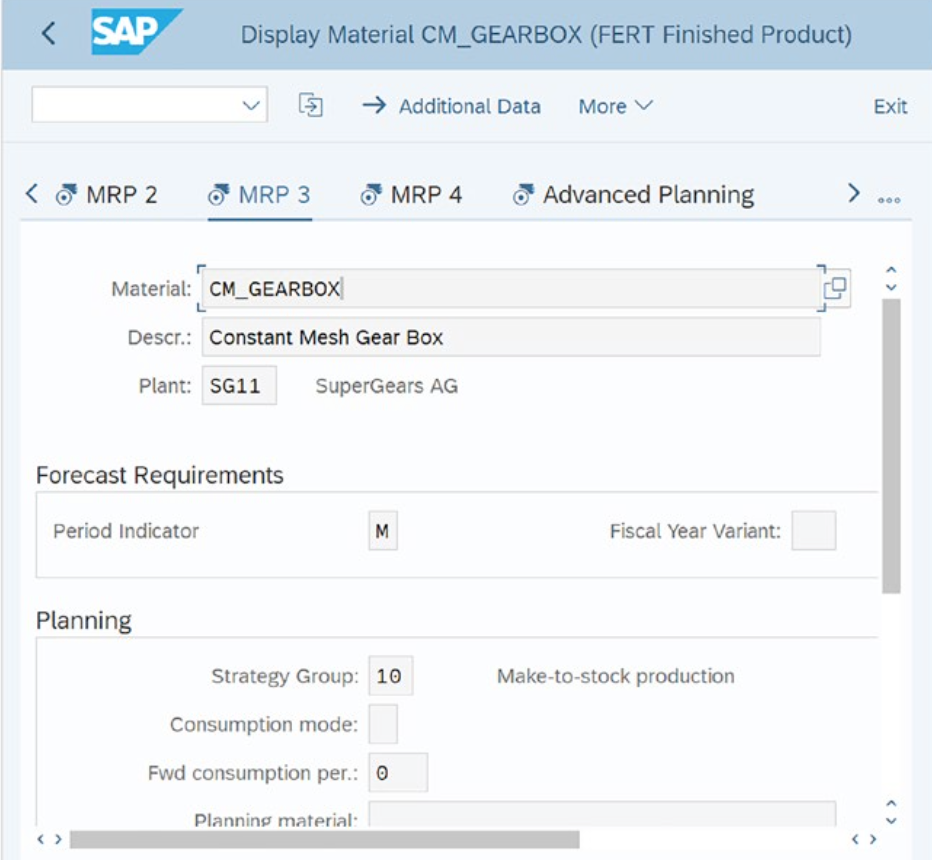
For Strategy 10, production is based entirely on forecasts. For instance, if the PIRs for a month total 300 units and the stock is 200, a planned order for 100 units will be generated to cover the shortfall. In contrast, Strategy 40 adjusts PIRs dynamically based on customer orders, ensuring demand flexibility.
Make-to-Order Strategies
In Make-to-Order (MTO), production is initiated only after receiving customer orders. Each sales order creates specific stock and requirements.
Strategy | Key Features |
---|---|
Strategy 20 | Each sales order is unique; production is directly linked to the sales order. Stock is displayed as sales order stock. |
Strategy 50 | PIRs drive the procurement of components, but final assembly is triggered only after receiving a sales order. |
For example, in Strategy 20, sales orders generate planned orders directly tied to the requirement. Once goods are produced, the stock is assigned to the sales order instead of being added to unrestricted inventory. Strategy 50 ensures that lower-level components are prepared in advance, while the final assembly is postponed until a customer order arrives, reducing lead times for customized products.
Planning with Final Assembly (Strategy 40)
Strategy 40 is widely used in industries that require flexible production planning. Customer orders consume PIRs, dynamically adjusting demand. For instance, if 300 units are forecasted but only 250 are ordered, the extra 50 units are added to stock. Conversely, if demand exceeds the forecast, the system generates additional planned orders.
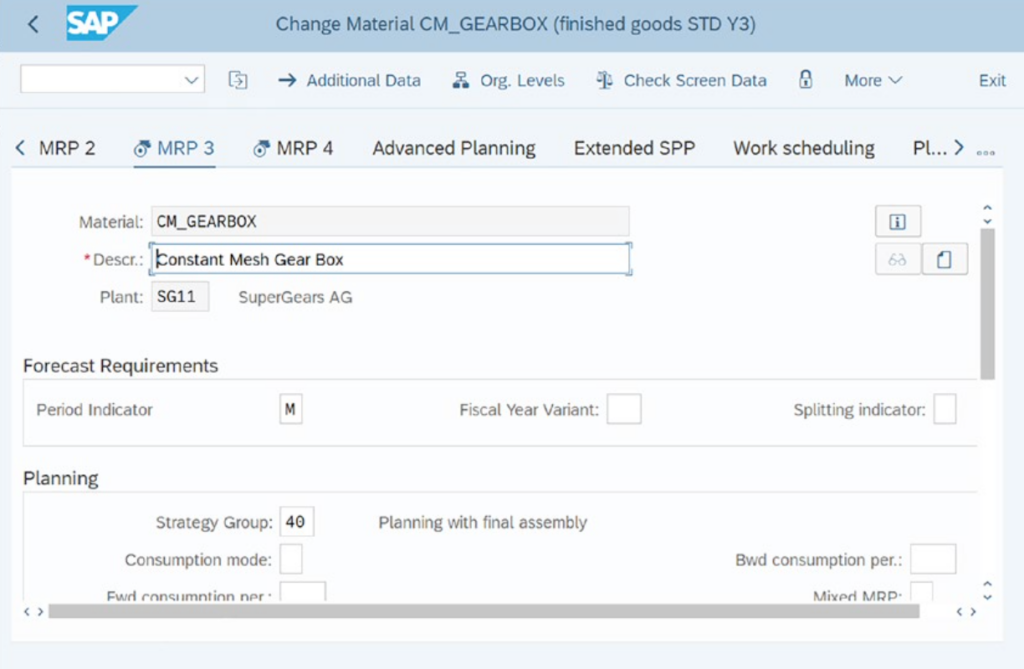
Scenario | Action |
---|---|
Demand < Forecast | Excess stock is retained in inventory. |
Demand > Forecast | New planned orders are created to meet additional demand. |
This approach enables businesses to react quickly to customer needs while maintaining efficient stock levels.
Benefits of Planning Strategies
Planning strategies in SAP PP enable businesses to tailor production processes to their operational requirements. Key benefits include:
- Flexibility: Supports both standardized (MTS) and customized (MTO) production.
- Efficiency: Optimizes stock utilization and reduces lead times.
- Scalability: Combines multiple strategies for complex manufacturing scenarios.
For example, a company may use MTO (Strategy 50) for final assembly while adopting MTS (Strategy 10) for sub-assemblies, balancing customization with production efficiency.
Planning strategies are the backbone of demand management in SAP PP, ensuring seamless integration between sales and production processes. They provide a structured approach to meeting both forecasted and customer-driven demands, enhancing operational agility and accuracy.