The Production Order Cycle in SAP PP represents the series of steps involved in managing and executing a production order, from creation to completion. It ensures efficient production planning and control while optimizing resource utilization and maintaining data accuracy.
Production Order Cycle in SAP PP
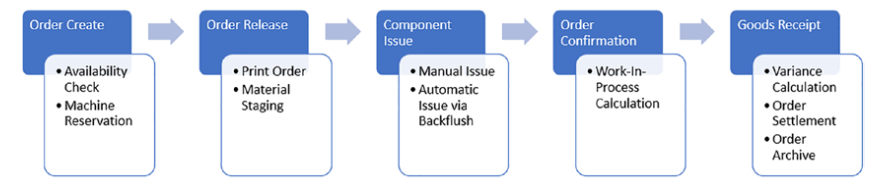
1. Order Creation
At this stage, the production order is created based on planned orders, sales orders, or other triggers. Key activities include:
- Availability Check: Ensures required materials, components, and resources (e.g., machines and tools) are available.
- Machine Reservation: Reserves the necessary work center resources to prevent scheduling conflicts.
Objective: To create a foundation for executing production while ensuring all resources are accounted for.
2. Order Release
Once the production order is reviewed and approved, it is released for execution. This step activates subsequent processes and enables shop floor activities. Key activities include:
- Print Order: Generates production documentation (e.g., job cards or instructions).
- Material Staging: Ensures all components and materials required for production are staged at the designated locations.
Objective: To prepare the order and materials for execution on the shop floor.
3. Component Issue
This step involves issuing components or materials to the production order. The system reduces inventory quantities as materials are consumed. Methods include:
- Manual Issue: Materials are manually issued to the order by posting goods movement.
- Automatic Issue (Backflush): Materials are automatically deducted from inventory based on predefined rules during production confirmation.
Objective: To ensure the production process has all necessary inputs.
4. Order Confirmation
At this stage, production is confirmed upon completion of tasks at each operation. Key activities include:
- Work-In-Process (WIP) Calculation: Tracks partially completed goods to evaluate progress and costs.
Objective: To confirm production progress and calculate associated costs accurately.
5. Goods Receipt
Once production is complete, the finished goods are received into inventory. Key activities include:
- Variance Calculation: Compares planned costs with actual production costs.
- Order Settlement: Allocates costs to appropriate cost centers or accounts.
- Order Archiving: Closes and archives the production order after settlement.
Objective: To finalize production and record the finished product in inventory.
Summary of the Production Order Cycle
Stage | Key Activities | Objective |
---|---|---|
Order Creation | Availability check, machine reservation | Prepare resources for production |
Order Release | Print order, material staging | Authorize and prepare for execution |
Component Issue | Manual/automatic material issue | Provide required inputs to production |
Order Confirmation | Confirm production, calculate WIP | Track progress and costs |
Goods Receipt | Record finished goods, variance calculation, settlement | Finalize production and update inventory |
This structured cycle ensures seamless coordination between planning, execution, and reporting, making production management efficient and transparent for users.