Production Orders in SAP PP are a central component of the manufacturing process in the SAP Production Planning (PP) module. They serve as detailed instructions for producing a specific quantity of a material within a defined timeframe. Understanding how to create, process, and manage production orders is essential for both beginners and advanced SAP users involved in production planning and execution.
Introduction to Production Orders in SAP PP
This SAP PP tutorial provides a professional and detailed guide on Production Orders in SAP PP, covering the entire lifecycle from creation to completion. It includes step-by-step instructions on using key transaction codes and explains essential concepts like Goods Issue with practical examples.
1 Production Order Lifecycle
1.1 Overview of the Production Order Lifecycle
The Production Order Lifecycle in SAP PP encompasses all the phases a production order goes through, from its initial creation to final completion. Managing this lifecycle effectively ensures that manufacturing processes are planned, executed, and monitored efficiently.
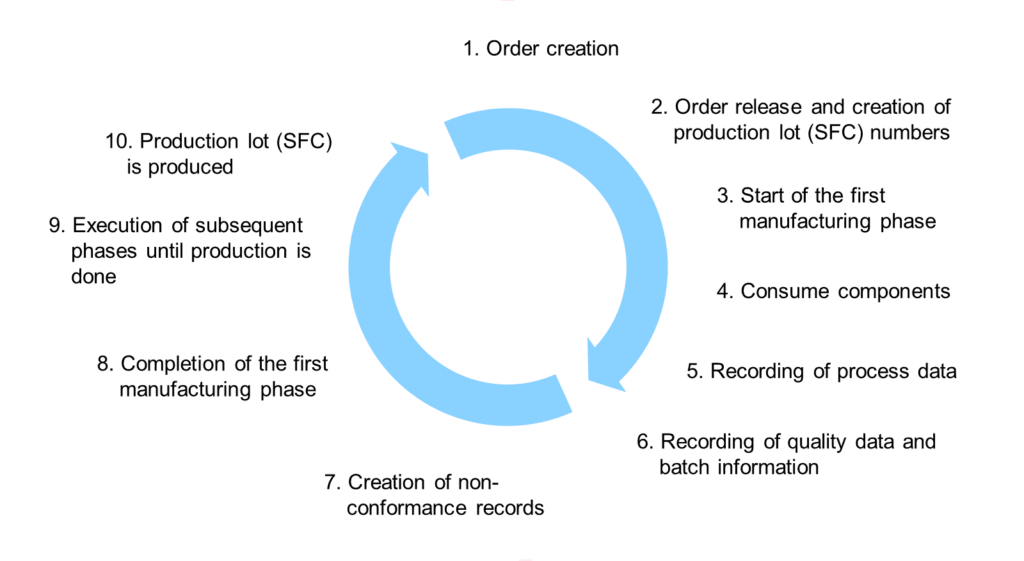
Key Phases:
- Creation: Defining the production order with all necessary details.
- Release: Authorizing the order for production execution.
- Goods Issue: Issuing raw materials and components required for production.
- Execution: Carrying out the production activities.
- Confirmation: Recording the completion of production operations.
- Goods Receipt: Receiving the finished goods into inventory.
- Settlement and Closure: Calculating costs and closing the order.
1.2 Stages of a Production Order
Stage 1: Creation
- Define Material and Quantity: Specify the material to be produced and the quantity.
- Assign BOM and Routing: Link the Bill of Materials (BOM) and routing to the order.
Stage 2: Release
- Authorize Production: Release the order to permit production activities.
- Enable Goods Movements: Allow posting of goods issues and receipts.
Stage 3: Goods Issue
- Issue Components: Withdraw raw materials and components from inventory.
- Update Inventory: Reduce stock levels of issued materials.
Stage 4: Execution
- Perform Operations: Execute production operations as per the routing.
- Utilize Work Centers: Use designated machines and labor.
Stage 5: Confirmation
- Record Progress: Confirm completed operations and quantities.
- Capture Actual Data: Log actual times, quantities, and activities.
Stage 6: Goods Receipt
- Receive Finished Goods: Post the produced goods into inventory.
- Update Order Status: Reflect production completion.
Stage 7: Settlement and Closure
- Settle Costs: Allocate costs to cost centers or profitability segments.
- Close Order: Mark the order as complete to prevent further changes.
2 Creation and Processing of Production Orders
SAP PP provides specific transaction codes for managing production orders. The primary transactions are CO01 (Create), CO02 (Change), and CO03 (Display).
2.1 CO01: Create Production Order
Purpose:
- To create a new production order with detailed instructions for production.
Example Scenario:
- You need to produce 100 units of Material FG-100 at Plant 1100.
Step-by-Step Guide:
- Access Transaction CO01
- Enter CO01 in the SAP command field and press Enter.
- Enter Initial Order Data
- Order Type: Use PP01 for standard production orders.
- Material: Enter FG-100.
- Plant: Enter 1100.
- Set Quantity and Dates
- Total Quantity: Enter 100 units.
- Basic Start Date: Enter the planned start date (e.g., 2024-11-25).
- Basic Finish Date: Enter the planned end date (e.g., 2024-11-30).
- Review BOM and Routing
- BOM Explosion: Ensure components are correctly listed.
- Routing Selection: Confirm operations are assigned.
- Schedule the Order
- Choose scheduling parameters (e.g., backward or forward scheduling).
- Click on Dates/Qtys to verify scheduled dates.
- Save the Production Order
- Click the Save icon or press Ctrl+S.
- The system generates a production order number (e.g., 10001234).
Notes:
- Ensure all master data (material, BOM, routing) is accurately maintained.
- The order cannot be released if mandatory data is missing.
2.2 CO02: Change Production Order
Purpose:
- To modify details of an existing production order.
Common Changes:
- Adjusting production quantities.
- Changing production dates.
- Modifying components or operations.
Step-by-Step Guide:
- Access Transaction CO02
- Enter CO02 in the SAP command field and press Enter.
- Enter Production Order Number
- Input the order number (e.g., 10001234) and press Enter.
- Navigate to the Relevant Tab
- Header: Change order header details.
- Operations: Modify operations or work centers.
- Components: Adjust component quantities or replacements.
- Make Necessary Changes
- For example, change the total quantity from 100 to 120 units.
- Save the Changes
- Click the Save icon or press Ctrl+S.
Notes:
- Changes may be restricted after certain statuses (e.g., after confirmation).
- Verify that changes are feasible within the production schedule.
2.3 CO03: Display Production Order
Purpose:
- To view production order details without the ability to modify them.
Step-by-Step Guide:
- Access Transaction CO03
- Enter CO03 in the SAP command field and press Enter.
- Enter Production Order Number
- Input the order number (e.g., 10001234) and press Enter.
- Review Order Information
- Order Header: View overall order data.
- Operations: See the list of operations and their statuses.
- Components: Check required materials and quantities.
- Costs: Review planned versus actual costs.
- Exit Display Mode
- Click the Back button or press F3 to exit.
Notes:
- Use CO03 for auditing purposes or to provide information to other departments.
- Display mode ensures data integrity by preventing unauthorized changes.
3 Goods Movement in Production
Goods movements are essential to reflect the flow of materials in production. Goods Issue (GI) is particularly important as it records the consumption of components for production orders.
3.1 Goods Issue (GI) Concept
Definition:
- Goods Issue is the process of withdrawing materials from inventory for use in production.
- It reduces inventory levels and assigns material costs to the production order.
Importance:
- Inventory Accuracy: Maintains correct stock levels.
- Cost Allocation: Ensures material costs are accurately captured.
- Production Tracking: Reflects actual consumption of materials.
Types of Goods Issue:
- Manual Goods Issue: Performed manually via transactions like MIGO.
- Automatic Goods Issue (Backflushing): Occurs automatically during operation confirmation.
3.2 Processing Goods Issue Using MIGO
Purpose:
- To manually post the goods issue of components to a production order.
Example Scenario:
- Issue Component RM-200 to Production Order 10001234 for 200 units.
Step-by-Step Guide:
- Access Transaction MIGO
- Enter MIGO in the SAP command field and press Enter.
- Select Goods Issue
- In the Transaction field, select Goods Issue.
- In the Reference field, choose Order.
- Enter Reference Details
- Order: Enter 10001234.
- Press Enter to retrieve order information.
- Verify and Edit Item Details
- Material: Confirm RM-200 is listed.
- Quantity: Ensure the quantity is 200 units.
- Storage Location: Enter the location from which the material is issued.
- Movement Type: Confirm it is 261 (Goods Issue for Order).
- Check Document
- Click on Check to validate the data for errors.
- Post the Goods Issue
- Click the Post button or press Ctrl+S.
- A material document number is generated confirming the posting.
Notes:
- Ensure sufficient stock is available in the specified storage location.
- Any discrepancies in quantities or materials should be resolved before posting.
Impact of Goods Issue:
- Inventory Update: Reduces stock of the issued material.
- Cost Posting: Allocates material costs to the production order.
- MRP Update: Adjusts material requirements planning data.
4 Conclusion
Managing Production Orders in SAP PP is vital for efficient manufacturing operations. This tutorial provided a comprehensive guide on the lifecycle of production orders, including creation, modification, and goods movement processes. By mastering these concepts and transaction codes, users can ensure accurate production planning, execution, and cost management.
Key Takeaways:
- Understanding the Lifecycle: Familiarity with each stage ensures effective production control.
- Transaction Proficiency: Using CO01, CO02, CO03, and MIGO efficiently is essential for daily operations.
- Accurate Goods Movements: Proper handling of goods issues maintains inventory accuracy and cost control.
- Real-World Application: Practical examples aid in applying concepts to actual business scenarios.
5 Further Reading and Resources
- SAP Help Portal: Official documentation on SAP PP functionalities.
- SAP Learning Hub: Access to training courses and learning materials.
- Production Planning with SAP S/4HANA: Books and guides on advanced planning techniques.
- SAP Community Network: Forums for discussions with SAP professionals.
For any questions or assistance with production orders in SAP PP, please contact your system administrator or SAP support team.