In this SAP tutorial, you will Learn about the three main production types in SAP Production Planning (PP): Discrete Manufacturing, Process Manufacturing, and Repetitive Manufacturing. Understand their features, suitable industries, and how to choose the right production type for your business needs.
Production Planning (PP) in SAP supports different types of production processes to meet various manufacturing requirements. Understanding these production types is essential for effectively planning, scheduling, and managing production activities based on the unique requirements of different industries.
Introduction to Production Types in SAP PP
In SAP PP, the main production types include:
- Discrete Manufacturing
- Process Manufacturing
- Repetitive Manufacturing (REM)
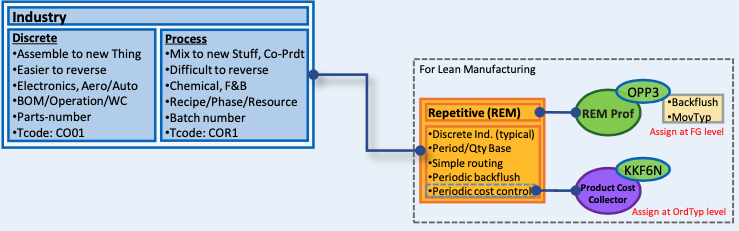
Each of these production types has its unique characteristics and is used in specific scenarios. In this tutorial, we will cover the details of each production type, including their features, processes, and relevant SAP transaction codes (Tcodes).
1 Discrete Manufacturing
Overview of Discrete Manufacturing
Discrete Manufacturing is characterized by the production of distinct items, such as cars, electronic devices, or machinery. The production process is typically order-based, and the final product can be counted and identified as separate units. Each product unit may have different specifications, and it is often easier to reverse or modify the production process.
Discrete manufacturing is commonly used in industries such as automotive, electronics, and machinery manufacturing.
Key Features
- Production is based on individual orders.
- Products can be identified as separate units.
- Easier to modify or reverse production orders.
- Bills of Materials (BOM) and Routings are key elements of the process.
Key Tcodes for Discrete Manufacturing
- CO01: Create Production Order
- CO02: Change Production Order
- CO03: Display Production Order
These Tcodes are used to manage production orders, which define the specific steps, materials, and work centers involved in manufacturing a product.
2 Process Manufacturing
Overview of Process Manufacturing
Process Manufacturing is used for products that are produced by mixing, refining, or chemical processing. It is used for goods that cannot be easily disassembled into their basic components, and the production is typically continuous or batch-based. Process manufacturing is common in industries such as chemicals, pharmaceuticals, food, and beverages.
In SAP PP, process manufacturing is managed through Process Orders, which are similar to production orders but are specifically designed to handle the complexities of process-based production.
Key Features
- Production is often continuous or based on batches.
- The final product cannot be easily broken down into its components.
- Uses Recipes instead of Routings to define the production process.
- Co-products and by-products are common.
Key Tcodes for Process Manufacturing
- COR1: Create Process Order
- COR2: Change Process Order
- COR3: Display Process Order
These Tcodes help manage process orders, which specify the resources, operations, and materials required to complete the production process.
3 Repetitive Manufacturing (REM)
Overview of Repetitive Manufacturing
Repetitive Manufacturing (REM) is used for products that are produced on a regular basis, often in high volumes. It is suited for environments where the same product is produced over a long period, and production is based on periods or quantities rather than individual orders. REM is commonly used in industries such as consumer goods and automotive parts manufacturing.
In REM, the production process is simplified by reducing the need for detailed production orders. Instead, production is driven by planned orders and demand management.
Key Features
- Production is based on quantities or periods rather than individual orders.
- Simplified production process with fewer documentation requirements.
- Uses Production Versions to determine the appropriate production line or method.
- Backflushing is used to automate inventory postings.
Key Tcodes for Repetitive Manufacturing
- MF50: Planning Table for Repetitive Manufacturing
- MFBF: Backflush
These Tcodes are used to manage the production schedule and automate inventory postings, ensuring that materials are consumed and goods are received automatically during production.
Choosing the Right Production Type
Summary of Manufacturing Industry Types
The manufacturing industry can be broadly classified into Discrete Manufacturing and Process Manufacturing. Discrete manufacturing involves producing products that can be disassembled into their original components, while process manufacturing involves transforming raw ingredients into new products using special processes. The table below summarizes the characteristics and suitable industries for each production type.
The choice of production type in SAP PP depends on the nature of the product being manufactured and the specific requirements of the business. Here is a summary to help you determine which production type may be suitable for your needs:
Production Type | Suitable Industries | Key Characteristics |
---|---|---|
Discrete Manufacturing | Automotive, Electronics | Order-based, distinct units, BOM, Routing |
Process Manufacturing | Chemicals, Pharmaceuticals | Batch-based, continuous, Recipes, Co-products |
Repetitive Manufacturing | Consumer Goods, Automotive Parts | High-volume, period-based, Production Versions |
Conclusion
Understanding the different production types in SAP PP is crucial for selecting the right approach to meet your manufacturing requirements. Whether you are dealing with individual, distinct items in Discrete Manufacturing, continuous production in Process Manufacturing, or high-volume production in Repetitive Manufacturing, SAP PP provides the tools needed to manage these processes effectively.
By leveraging the appropriate production type and using the relevant Tcodes, businesses can optimize their production planning, reduce costs, and ensure timely delivery of products.