In the SAP Material Master Record, the MRP1 view is crucial for planning and managing material requirements. It contains three main sections:
- General Data
- MRP Procedure
- Lot Size Data
Understanding these sections and their key fields helps in effective material planning and procurement. This guide delves into each section, explaining their purposes and important parameters.
Overview of the MRP1 View
The MRP1 view is part of the Material Requirements Planning (MRP) data in the material master. It influences how the material is planned, ordered, and produced within the organization.
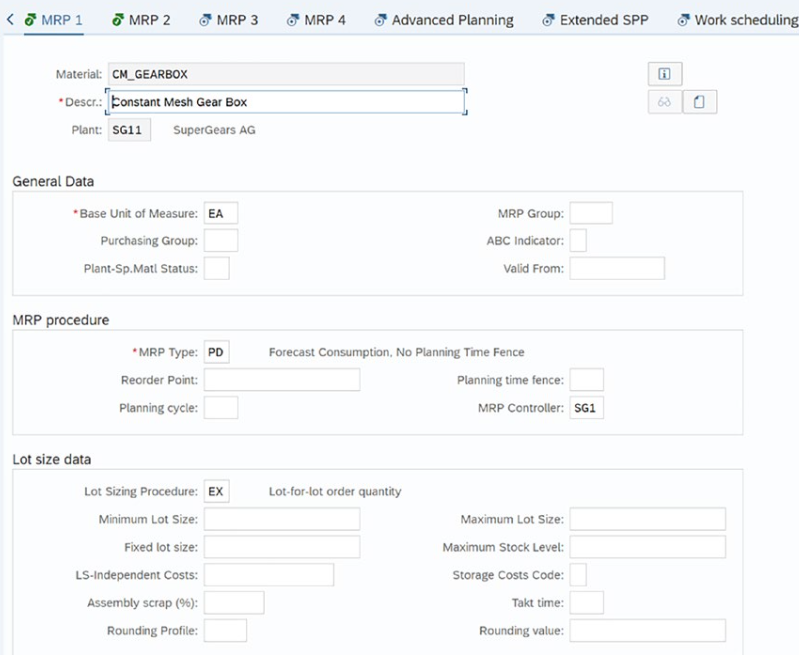
1 General Data
The General Data section contains fundamental information that applies to the material across different planning scenarios.
Key Fields:
- Base Unit of Measure (UoM):
- Description: The unit in which the material’s stock is managed.
- Purpose: Ensures consistency in inventory management, even if different departments use alternative units of measure.
- Example: Pieces (PC), Kilograms (KG), Liters (L).
- MRP Group:
- Description: Groups materials with similar planning parameters.
- Purpose: Allows collective management of MRP parameters like planning strategy, consumption mode, and order types.
- Example: MRP Group “FERT” for finished goods.
- Purchasing Group:
- Description: Identifies the buyer or group responsible for procurement.
- Purpose: Facilitates communication and responsibility assignment in purchasing processes.
- Example: Purchasing Group “001” for electronics components.
- ABC Indicator:
- Description: Classifies materials based on their consumption value.
- Purpose: Prioritizes materials in planning and inventory management.
- Categories:
- A: High consumption value (most important).
- B: Medium consumption value.
- C: Low consumption value (least important).
- Plant-Specific Material Status:
- Description: Controls the material’s usability in specific business processes.
- Purpose: Restricts or allows material usage in areas like purchasing, MRP, or production.
- Example: Status “01” might block the material from being purchased but allow it in production.
Table 1: ABC Classification Example
ABC Indicator | Consumption Value (%) | Importance |
---|---|---|
A | 70% | Most important |
B | 20% | Moderate |
C | 10% | Least important |
2 MRP Procedure
The MRP Procedure section defines how the material is planned and which planning strategies are applied.
Key Fields:
- MRP Type:
- Description: Determines the planning method for the material.
- Purpose: Controls whether the material is planned using MRP, consumption-based planning, or not planned.
- Common MRP Types:
- PD: Standard MRP.
- VB: Manual Reorder Point Planning.
- V1: Automatic Reorder Point Planning.
- VV: Forecast-Based Planning.
- Reorder Point:
- Description: The stock level that triggers a new procurement proposal.
- Purpose: Ensures timely replenishment of stock.
- Applicable When: Using reorder point planning (e.g., MRP type VB or V1).
- Planning Time Fence:
- Description: A period during which the planning system does not automatically change procurement proposals.
- Purpose: Protects short-term plans from automatic changes.
- Example: A time fence of 7 days means the system won’t alter orders within the next week.
Table 2: Common MRP Types and Their Descriptions
MRP Type | Planning Method |
---|---|
PD | Materials Requirements Planning |
VB | Manual Reorder Point Planning |
V1 | Automatic Reorder Point Planning |
VV | Forecast-Based Planning |
Understanding MRP Types:
- Materials Requirements Planning (MRP):
- Usage: For materials with dependent and independent requirements.
- Function: Plans material based on demand forecasts and production schedules.
- Consumption-Based Planning (CBP):
- Types:
- Reorder Point Planning: Triggers procurement when stock falls below the reorder point.
- Forecast-Based Planning: Uses historical consumption data to predict future needs.
- Time-Phased Planning: Plans procurement at regular intervals.
- No Planning:
- MRP Type ‘ND’: The material is not included in MRP runs.
3 Lot Size Data
The Lot Size Data section determines the quantities for procurement and production orders.
Key Fields:
- Lot Size:
- Description: Specifies how the procurement quantity is calculated.
- Purpose: Optimizes order quantities based on factors like demand, costs, and storage.
- Lot Size Procedures:
- Static Lot Sizes: Fixed quantities or lot-for-lot.
- Periodic Lot Sizes: Consolidates requirements over periods (daily, weekly).
- Optimum Lot Sizes: Calculates economic order quantities.
- Minimum Lot Size:
- Description: The smallest quantity that can be procured or produced.
- Purpose: Ensures economic order quantities and avoids unprofitable small orders.
- Example: A minimum lot size of 100 units.
- Maximum Lot Size:
- Description: The largest quantity allowed per order.
- Purpose: Prevents overstocking and considers capacity constraints.
- Example: A maximum lot size of 1,000 units.
- Rounding Profile:
- Description: Adjusts order quantities to predefined increments.
- Purpose: Aligns quantities with packaging sizes or transportation units.
- Example: Orders rounded to the nearest pallet size.
- Assembly Scrap:
- Description: Percentage of material expected to be lost during production.
- Purpose: Increases procurement quantities to account for losses.
- Example: 5% assembly scrap increases an order of 100 units to 105 units.
Table 3: Examples of Lot Size Procedures
Lot Size Key | Description |
---|---|
EX | Lot-for-Lot Order Quantity |
FX | Fixed Lot Size |
HB | Replenish to Maximum Stock Level |
WB | Weekly Lot Size |
SP | Periodic Lot Size with Spacing |
Understanding Lot Size Procedures:
- Static Lot Sizes:
- Lot-for-Lot (EX): Orders match exact requirement quantities.
- Fixed Lot Size (FX): Orders are always a fixed quantity.
- Periodic Lot Sizes:
- Daily (TD), Weekly (WB), Monthly (MB): Consolidates requirements within the period.
- Optimum Lot Sizes:
- Economic Order Quantity (EOQ): Calculates the most cost-effective order size.
- Part Period Balancing (PP): Balances ordering and holding costs.
Practical Example
Let’s consider a material that is manufactured in-house and requires careful planning.
General Data:
- Base Unit of Measure: Pieces (PC)
- MRP Group: FERT (Finished Goods)
- Purchasing Group: Not applicable (since it’s produced in-house)
- ABC Indicator: A (High consumption value)
- Plant-Specific Material Status: Released for all processes
MRP Procedure:
- MRP Type: PD (Standard MRP)
- Reorder Point: Not applicable (since it’s MRP type PD)
- Planning Time Fence: 5 days
Lot Size Data:
- Lot Size: EX (Lot-for-Lot)
- Minimum Lot Size: 100 PC
- Maximum Lot Size: 1,000 PC
- Assembly Scrap: 2%
Scenario:
- Demand: 450 units needed
- Calculation:
- Accounting for Assembly Scrap:
- Required Quantity = Demand / (1 – Scrap %)
- Required Quantity = 450 / (1 – 0.02) ≈ 459.18
- Rounded to 460 units
- Order Quantity:
- Since the lot size is Lot-for-Lot, the order quantity is 460 units.
Importance of the MRP1 View
- Effective Planning: Ensures materials are available when needed without overstocking.
- Cost Optimization: Balances ordering costs with holding costs through appropriate lot sizing.
- Production Efficiency: Accounts for scrap and other production losses.
- Supply Chain Coordination: Aligns procurement and production schedules.
Tips for Managing MRP1 Data
- Regular Review: Update MRP parameters to reflect changes in demand or production processes.
- Collaborate with Stakeholders: Work with production planners, procurement specialists, and inventory managers.
- Utilize Analytics: Analyze consumption patterns to fine-tune reorder points and lot sizes.
- Maintain Data Accuracy: Ensure fields like lead times and scrap percentages are current.
Conclusion
The MRP1 view is a foundational element in the SAP Material Master Record for effective material planning. By carefully setting parameters in the General Data, MRP Procedure, and Lot Size Data sections, organizations can optimize their inventory levels, reduce costs, and enhance production efficiency. Regular maintenance and collaboration among departments are key to leveraging the full benefits of the MRP1 view.
Further Reading:
- SAP Help Portal: Detailed explanations of MRP parameters.
- Material Requirements Planning Best Practices: Industry standards for MRP settings.
- Inventory Management Strategies: Techniques for optimizing stock levels.