In SAP’s Material Requirements Planning (MRP) system, the MRP3 view in the Material Master is an essential component. This view provides more detailed control over how materials are planned, forecasted, and checked for availability, allowing for plant-specific configurations that streamline production and inventory processes. In this post, we’ll walk through the MRP3 view’s four main sections—Forecast Requirements, Planning, Availability Check, and Plant-Specific Configuration—exploring each section’s purpose and key fields for effective configuration.
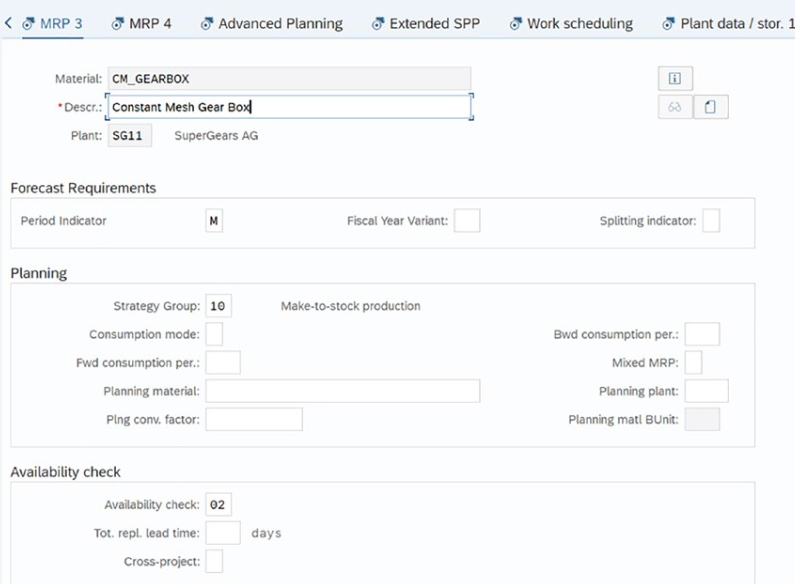
Why the MRP3 View Matters in SAP
The MRP3 view enables material planners to implement precise planning and inventory controls. Each section in the MRP3 view addresses specific aspects of forecasting, availability, and configuration. This view is especially valuable for organizations with complex production processes, allowing them to balance demand, manage stock, and avoid production delays.
Key Sections in the MRP3 View
1 Forecast Requirements
The Forecast Requirements section in MRP3 is all about predicting future demand based on historical data. By understanding forecast requirements, companies can better anticipate inventory needs and avoid both stockouts and overstock situations.
Key Fields
- Strategy Group:
- Purpose: Determines the planning strategy, guiding whether the material is produced based on forecasted demand (make-to-stock) or specific customer orders (make-to-order).
- Examples:
- 10 – Make-to-stock production: Production is driven by forecasted demand.
- 20 – Make-to-order production: Production is aligned with specific customer orders.
- Consumption Mode:
- Purpose: Controls how forecasted demand is adjusted based on actual orders, either by using forecasts before or after the demand date.
- Types:
- Backward Consumption: Allocates demand to forecasted requirements prior to the order date.
- Forward Consumption: Allocates demand to forecasted requirements after the order date.
- Backward and Forward Consumption Periods:
- Purpose: Specifies the time periods (in days) for consuming forecast requirements.
- Example: A backward period of 10 days allows forecasts to be adjusted based on customer orders received up to 10 days prior to the planned demand date.
Example Configuration:
Field | Setting | Explanation |
---|---|---|
Strategy Group | 10 | Make-to-stock production |
Consumption Mode | Backward | Uses forecasts before demand date |
Backward Consumption Period | 10 | Adjusts for customer orders within 10 days |
2 Planning
In the Planning section, SAP users define parameters for how a material is planned. This allows companies to maintain consistent production schedules by anticipating demand over a set time frame and activating forecasts as needed.
Key Fields
- Planning Strategy:
- Purpose: Determines the overall production approach, helping decide if production is initiated based on forecasted demand or specific customer needs.
- Planning Horizon:
- Purpose: Specifies the time frame for planning, ensuring adequate lead time for material availability.
- Example: A 180-day planning horizon helps account for long-lead materials and future production needs.
- Forecast Indicator:
- Purpose: Signals if forecasting is active for the material, useful for items with stable, predictable demand.
Example Configuration:
Field | Setting | Explanation |
---|---|---|
Planning Horizon | 180 | Ensures a 180-day planning period |
Forecast Indicator | Yes | Activates forecasting |
3 Availability Check
The Availability Check section ensures that materials are in stock and ready to meet demand. It is particularly useful for confirming material availability during sales order creation, production orders, or purchase requisitions.
Key Fields
- Availability Check Group:
- Purpose: Specifies the type of availability check, ensuring materials are checked based on either cumulative or individual requirements.
- Options:
- 01 – Daily Requirements: Combines all daily demands for a single availability check.
- 02 – Individual Requirements: Checks each requirement, such as a specific sales order or production order.
- Scope of Check:
- Purpose: Defines the types of stock and MRP elements (e.g., stock, planned orders) to be included in the availability check, ensuring a comprehensive view of stock and demand.
Example Availability Check Groups
Availability Check Group | Description |
---|---|
01 | Daily Requirements |
02 | Individual Requirements |
KP | No Availability Check |
4 Plant-Specific Configuration
The Plant-Specific Configuration section allows for customized planning parameters that can vary from one plant to another. This is helpful for companies with multiple production sites or plants, allowing for adjustments in procurement, inventory management, and storage based on local requirements.
Key Fields
- MRP Controller:
- Purpose: Assigns responsibility to an individual or team for overseeing material planning within the plant, ensuring accountability.
- Storage Location MRP Indicator:
- Purpose: Specifies whether MRP should be carried out for a material at a specific storage location, enabling location-based control.
- Special Procurement Type:
- Purpose: Defines unique procurement methods, such as subcontracting or in-plant production.
- Examples:
- Consignment: Material is held as consignment stock.
- Subcontracting: Material is produced by an external vendor.
Example Configuration:
Field | Setting | Explanation |
---|---|---|
MRP Controller | PL1 | Assigned to Planner responsible for production |
Storage Location MRP Indicator | No | Excludes storage location from MRP |
Special Procurement Type | In-house Production | Material is produced internally |
How MRP3 View Works in Practice
With the MRP3 view set up, the following process typically occurs:
- Forecasting: Based on the strategy group, forecast requirements are adjusted using past demand data. Forecasts are then adjusted against actual customer orders according to the consumption mode.
- Planning: Material requirements are calculated for the defined planning horizon, ensuring that materials are available for current and future production needs.
- Availability Check: During order creation, the system verifies that there is enough stock or planned production to meet the demand, factoring in any plant-specific requirements.
- Plant-Specific Configuration: Unique plant-based settings, such as special procurement types, storage location requirements, and MRP control assignments, are applied to refine the planning process.
Conclusion
The MRP3 view in the SAP Material Master is a powerful tool for detailed material planning, allowing organizations to control forecasted demand, manage stock availability, and tailor planning parameters at the plant level. By leveraging fields such as the Strategy Group, Planning Horizon, Availability Check Group, and Special Procurement Type, companies can ensure materials are available on time, optimize inventory levels, and streamline production.
By understanding the sections within the MRP3 view, SAP users can achieve better planning precision, avoid production delays, and enhance inventory management across different production plants.