Planned orders are essential components of SAP Production Planning (PP). They represent procurement proposals generated during the Material Requirements Planning (MRP) process or created manually to meet material requirements for in-house production. This guide provides an in-depth understanding of planned orders, including their creation, functionality, and usage in production planning.
In this SAP PP tutorial, you will learn about Planned Orders in SAP PP, their creation, scheduling, components overview, and conversion for efficient production planning. Simplify material management and ensure accurate manufacturing execution
What is a Planned Order in SAP PP?
A planned order in SAP PP is a request for the procurement or production of materials. It includes details such as:
- Material: The product to be produced.
- Quantity: The amount to be produced.
- Production Dates: Planned start and end dates.
Key Characteristics
- Procurement Proposal: Planned orders are not directly executable for production but must be converted into production orders for discrete and process industries.
- Repetitive Manufacturing: In repetitive manufacturing, planned orders with the PE Run-Schedule Quantity order type are directly used for production execution and cannot be converted to production orders.
Planned Order Creation
Planned orders can be created automatically by MRP or manually by the user.
1. Manual Creation
To create a planned order manually:
- Navigate to Logistics ➤ Production ➤ MRP ➤ Planned Order ➤ Create or use Transaction Code MD11.
- Specify a planned order profile, which defines parameters like order type, procurement type, and account assignment category.
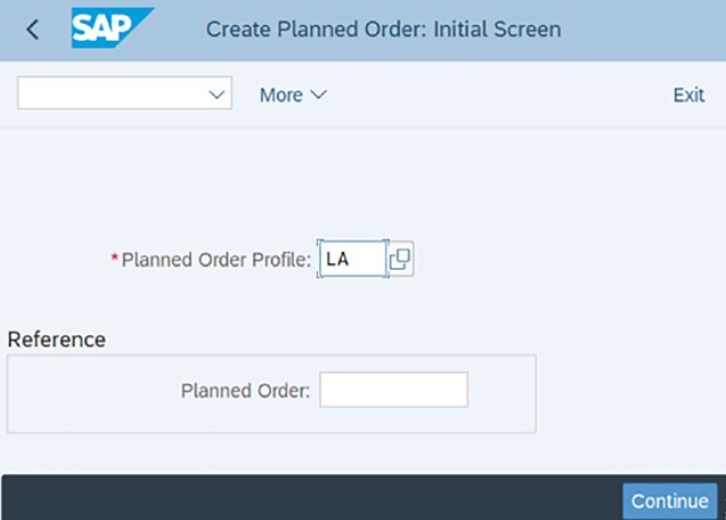
Order Types Table
Profile | Procurement Proposal Type | Procurement Type | Special Procurement Type | Account Assignment Category |
---|---|---|---|---|
KB | Standard purchase order | In-house procurement | Standard | General |
KD | Individual customer order | External procurement | Special customer orders | Customer-specific |
LA | Stock order | External procurement | Standard | General |
Structure of a Planned Order
Planned orders are divided into three key views: Header, Assignment, and Master Data.
1. Header View
The header contains three main sections:
- Quantities: Specifies order quantity and scrap quantity.
- Dates/Times:
- Basic Dates: Calculated using in-house production time. Accuracy is to the day.
- Production Dates: Calculated via lead time scheduling with accuracy to minutes/seconds, based on routing times like setup, processing, and queue times.
- Opening Date: Defines the buffer period for converting planned orders to production orders.
- Goods Receipt (GR) Processing Time: Includes the time for inspecting and storing materials after production.
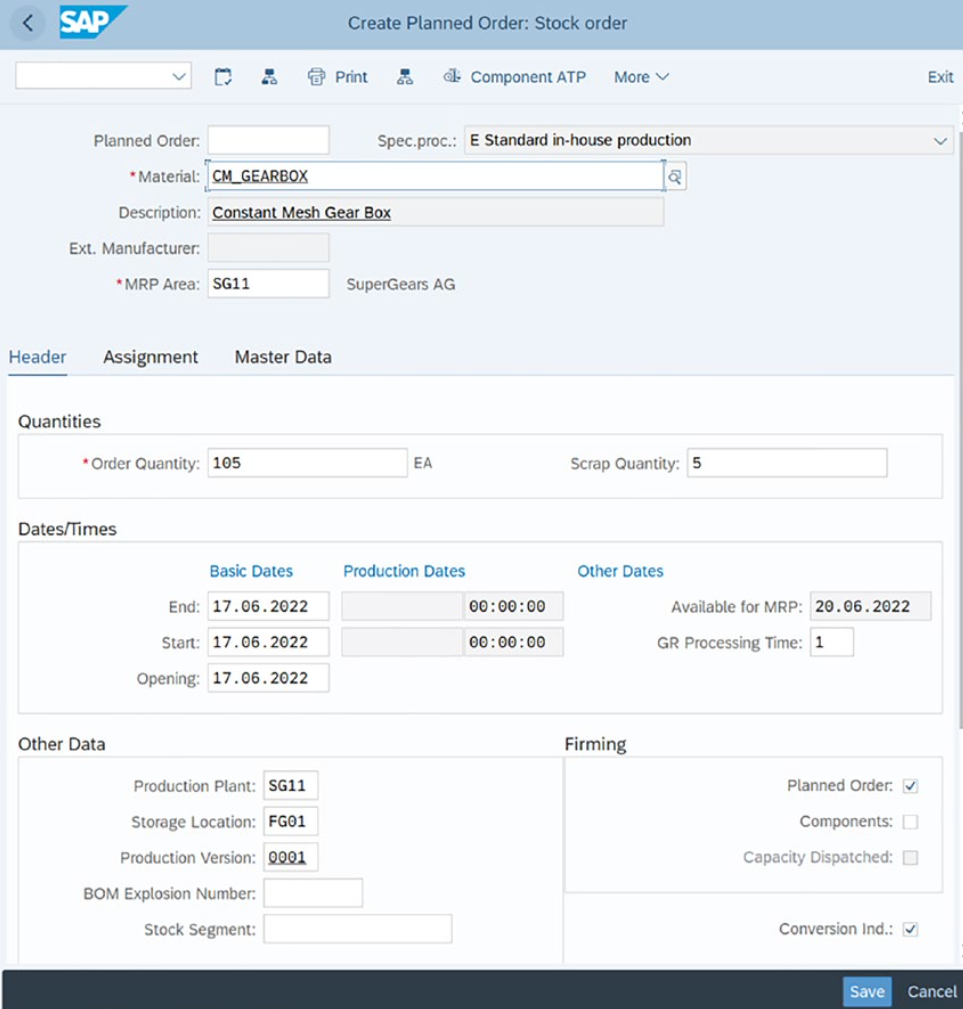
2. Assignment View
Details responsibilities and account assignments:
- Responsibility: Includes the MRP controller, production supervisor, and purchasing group.
- Account Assignment:
- Specifies the cost object, such as a cost center or sales order.
- Indicates special stock types like consignment stock or WBS elements in an engineer-to-order scenario.
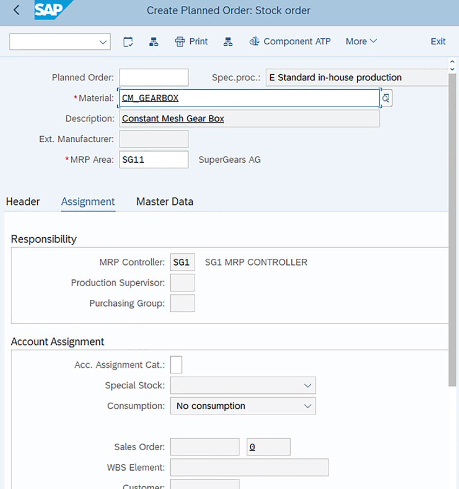
3. Master Data View
Displays data from the material master and BOM:
- Material Master: Includes MRP-relevant fields like procurement type and lead time.
- Bill of Material (BOM): Exploded based on the production version specified in the planned order.
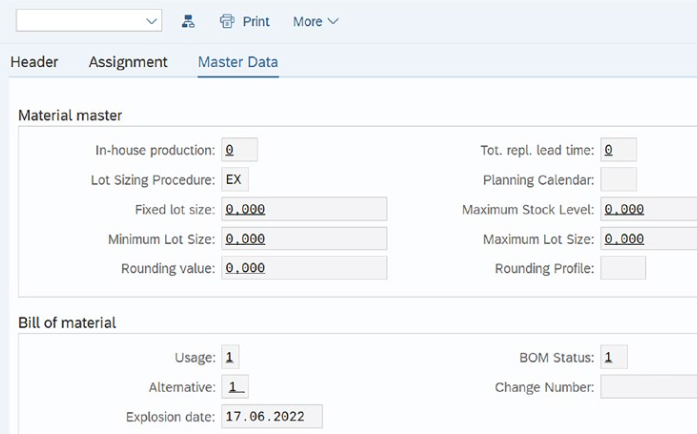
Scheduling a Planned Order in SAP PP
Scheduling a planned order calculates production dates and times based on routing. If basic scheduling was executed during the MRP run, you can manually schedule or reschedule the order by selecting the Schedule Planned Order option. The system applies lead time scheduling to determine accurate production dates and times, considering routing elements like setup, processing, and queue times.
Rescheduling is also possible if the order had been previously scheduled manually or during an MRP lead time scheduling run, ensuring the latest production dates are calculated
Conclusion
Planned orders in SAP PP are foundational for bridging the gap between material planning and production execution. Whether generated manually or automatically through MRP, they provide flexibility and precision in production planning.
Understanding their structure, creation, and management ensures smooth production processes and optimal material utilization. Proper configuration, such as defining order profiles and firming strategies, enhances their effectiveness in diverse manufacturing environments.