Routing in SAP PP defines the sequence of operations and processes required to manufacture a product. It outlines key details like operations, work centers, times for each task, required materials, and tools. Routing is crucial for efficient production planning, scheduling, and costing.
Key Elements of Routing in SAP PP?
Routing in SAP PP includes several critical elements that define the production process. These elements ensure smooth execution by specifying tasks, locations, timeframes, materials, and tools required for manufacturing. The table below summarizes the key elements, providing an overview of their roles in routing.
Element | Description |
---|---|
Operations | Defines tasks like machining, drilling, or assembly. Each operation is identified by a unique number (e.g., 0010). |
Work Centers | Specifies where operations are performed, such as assembly lines or machines. |
Production Times | Includes setup time, machine time, and labor time, crucial for scheduling and costing. |
Materials | Lists the components required for each operation, ensuring precise material allocation. |
Tools (PRT) | Specifies tools like molds or fixtures used during production. |
Routing Creation in SAP PP
Creating a routing in SAP PP involves defining the processes and resources required for production. You can use Transaction Code CA01 or navigate through Logistics ➤ Production ➤ Master Data ➤ Routings ➤ Standard Routings ➤ Create. The table below highlights the fields required for creating a routing.
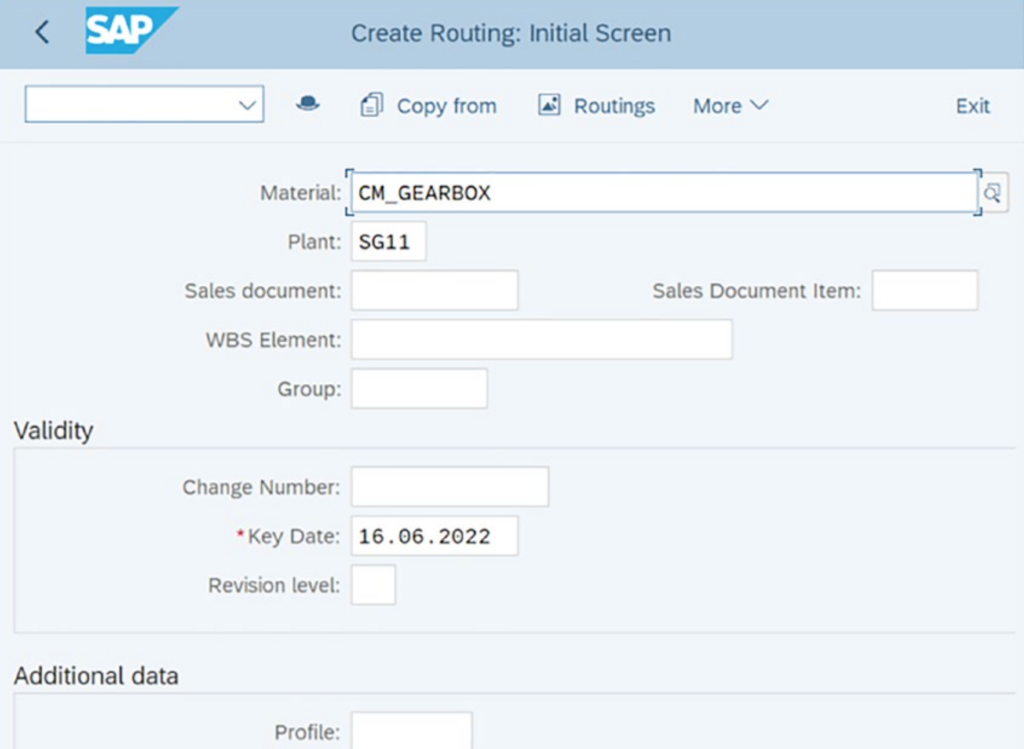
Field | Description |
---|---|
Material Number | The material for which the routing is created. |
Plant | Specifies the production plant. |
Key Date | The date from which the routing is valid. |
Group | A unique identifier for routing. |
Group Counter | Differentiates multiple routings for the same material or production process. |
Routing Status and Lot Size
Routing status controls its usability for production and costing, while lot sizes specify the quantity range for which a routing is valid. These parameters are critical for ensuring routing relevance to specific production scenarios, as shown in the table below.
Status | Usage |
---|---|
Created | Not usable in production orders. |
Released for Order | Usable in production orders but not for costing. |
Released for Costing | Usable for costing but not in production orders. |
Released (General) | Usable for both production orders and costing. |
Lot size defines the minimum and maximum quantities for which a routing is valid. For example:
Material | Group | Group Counter | Lot Size From | Lot Size To |
---|---|---|---|---|
Gear Assembly | 50000001 | 1 | 1 | 500 |
Gear Assembly | 50000001 | 2 | 501 | 1000 |
Scheduling and Overlapping
Routing incorporates scheduling to determine operation start and end times while managing capacity and resource allocation. Overlapping allows the next operation to begin before the current one finishes, optimizing lead times. The table below highlights key scheduling parameters.
Scheduling Parameter | Description |
---|---|
Setup Time | Time required to prepare machines for production. |
Queue Time | Time an order waits at the work center before being processed. |
Move Time | Time needed to transfer materials between operations. |
Overlapping | Allows the next operation to begin before the current one finishes, reducing overall lead time. |
Control Key and Component Allocation
The control key determines how operations are processed and managed in production. It controls parameters like scheduling, costing, and external processing. Components from the Bill of Materials (BOM) are allocated to specific operations in routing. This ensures materials are consumed only when required.
Control Key Parameter | Function |
---|---|
Scheduling | Determines if scheduling is performed on the work center. |
Capacity Requirements | Defines if capacity is calculated for the operation. |
Automatic Goods Receipt | Posts goods receipt automatically after confirmation. |
External Processing | Indicates that the operation is subcontracted to an external vendor. |
Example: Routing at SuperGears
At SuperGears, the production of gearboxes involves several operations: machining, drilling, and assembly. Each step is assigned to a specific work center, such as an assembly line.
Operation | Work Center | Setup Time | Machine Time | Labor Time |
---|---|---|---|---|
Machining | CM_MACH | 30 mins | 2 hrs | 1 hr |
Drilling | CM_DRILL | 20 mins | 1.5 hrs | 0.5 hrs |
Assembly | CM_ASSY | 10 mins | 3 hrs | 1.5 hrs |
By assigning tools and allocating BOM components, routing ensures smooth execution of production tasks. Overlapping operations further reduce lead times, improving overall efficiency.
Routing in SAP PP provides a comprehensive framework for defining production processes, ensuring precise scheduling, efficient material consumption, and accurate cost tracking. It is an indispensable tool for streamlined manufacturing.