Automating purchase orders (PO) is a game-changer for streamlining procurement processes. By enabling seamless integration between systems and minimizing manual intervention, businesses can save time, reduce errors, and enhance supplier relationships. This guide covers the essential steps, including configuring ALE data, activating automatic PO in item categories, and maintaining material sources and purchase info records.
With SAP’s powerful tools like VOV7, ME01, and ME11, automating POs ensures efficiency and accuracy, making your procurement processes faster, smarter, and more reliable.
Adding ALE Data for Purchase Order in Sales Organization
Application Link Enabling (ALE) is essential for integrating and transferring data between systems in distributed environments. Configuring ALE for purchase orders ensures seamless communication and automation across the sales organization.
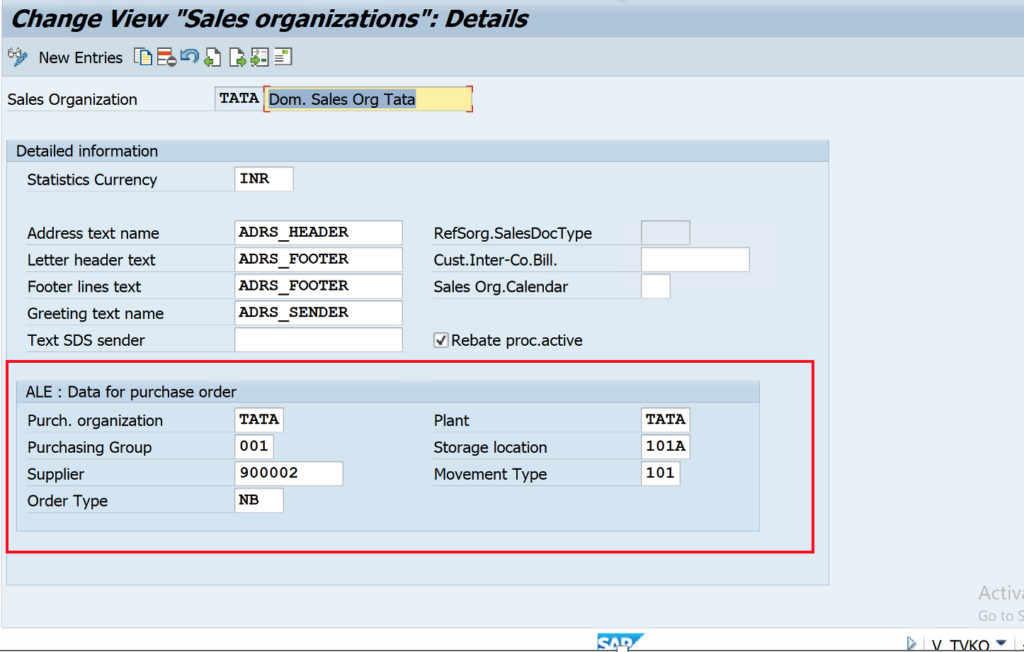
ALE (Application Link Enabling) data for purchase orders. Key fields include the sales organization “TATA,” associated plant, purchasing group (001), supplier (900002), storage location (101A), and movement type (101). The setup enables seamless integration for automated POs by linking the sales organization with the purchasing organization and supplier. Additionally, it includes text formatting fields, statistical currency (INR), and options for rebate processing and standard purchase order type (NB).
Step 1: Activate Automatic PO in Item Category (VOV7)
To enable automation, the Automatic PO setting must be activated in the Item Category. This ensures the system generates POs without manual intervention for specific categories.
- Steps to configure in VOV7:
- Navigate to Transaction Code VOV7.
- Locate the relevant item category.
- Enable the Automatic PO checkbox.
- Save the settings.
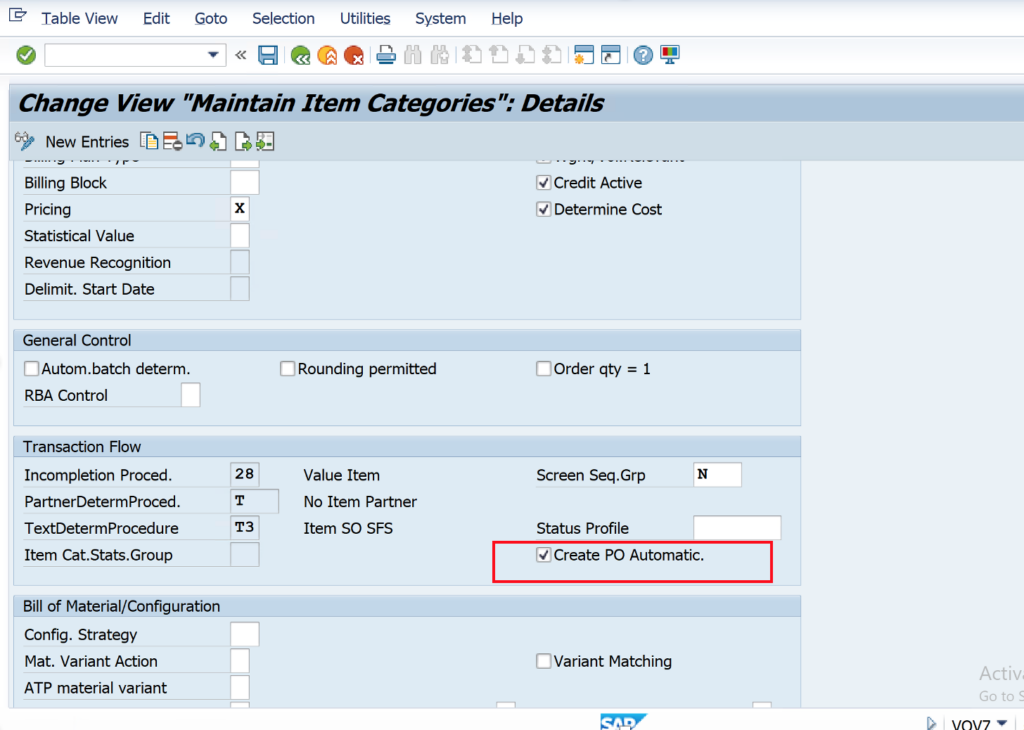
Step 2: Enable Automatic PO in Business Partner (BP)
The second step involves configuring the Purchasing View in the Business Partner (BP) master data. This step ensures that vendors or suppliers can process automated purchase orders.
- Steps:
- Open the Business Partner module.
- Navigate to the Purchasing View tab.
- Check the Automatic PO option.
- Save the changes.
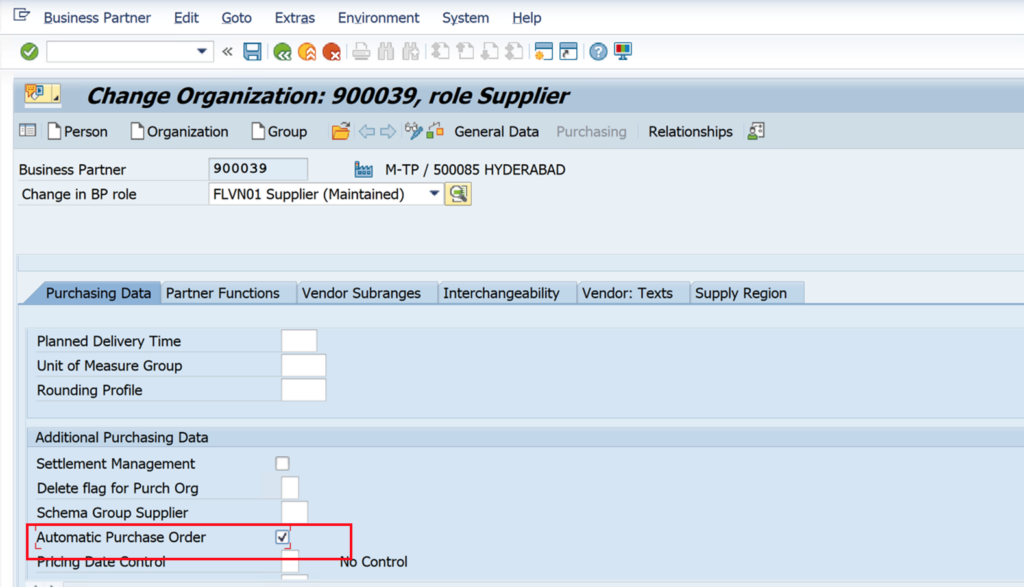
Step 3: Maintain Material Source (ME01)
Defining the material source is critical to identify the supplier for specific materials. Use Transaction Code ME01 for this step.
- Steps:
- Enter the material and plant information in ME01.
- Assign a valid supplier source.
- Save the source data.

Step 4: Maintain Purchase Info Record (ME11)
Purchase Info Records provide the system with vendor-specific data, including prices, terms, and conditions.
- Steps:
- Access Transaction Code ME11.
- Enter details like material, vendor, and purchasing organization.
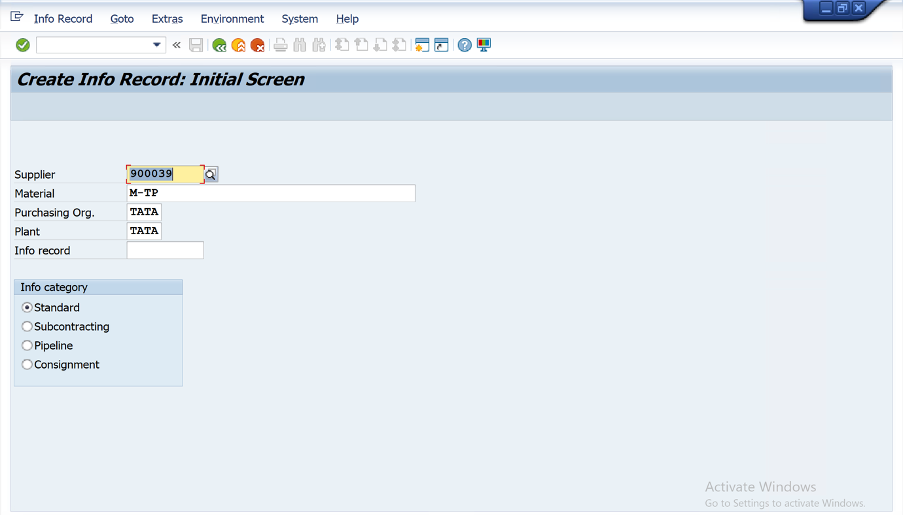
- Specify pricing and validity periods.
- Save the record.
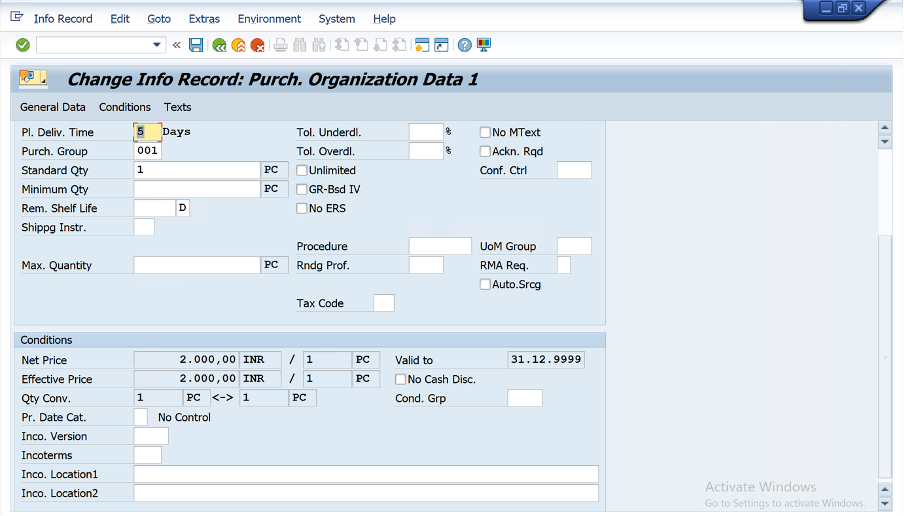
Table Summary of Configurations
Step | Transaction Code | Key Action |
---|---|---|
Activate Automatic PO | VOV7 | Enable Automatic PO in Item Category. |
Configure Purchasing | BP | Check Automatic PO in Purchasing View. |
Define Material Source | ME01 | Assign supplier for materials. |
Maintain Info Record | ME11 | Record vendor details and pricing. |
Benefits of Automating Purchase Orders
- Time Savings: Reduce manual work in repetitive tasks.
- Improved Accuracy: Minimize errors caused by manual entry.
- Streamlined Procurement: Ensure timely and efficient purchasing processes.
- Enhanced Supplier Relationships: Fulfill orders promptly with fewer discrepancies.
Conclusion
Automating POs ensures a smoother, faster procurement process. By following these steps and maintaining accurate master data, your organization can achieve higher efficiency and reduce costs.