Learn about Material Management in SAP, a module that optimizes procurement, inventory, and warehouse management processes. Streamline supply chain operations and improve efficiency
What is Material Management in SAP?
Material Management (MM) in SAP is a comprehensive module primarily focused on procurement, inventory management and material valuation. It ensures that materials are available to meet production needs, manages procurement processes, and maintains inventory at optimal levels. It is designed to facilitate efficient procurement and inventory management, crucial for maintaining an uninterrupted supply chain.
Key points in Material Management (MM)
Material Management (MM) include procurement process optimization, efficient inventory management to reduce costs and ensure timely availability of materials, vendor management for improved supplier relationships, and accurate material valuation for financial reporting.
MM’s integration with other SAP modules enhances overall business efficiency, making it indispensable for organizations looking to optimize their supply chain and procurement operations.
Material Management (MM) Core Functions
- Procurement Process: Managing the procurement activities from purchase requisition to purchase order and vendor selection.
- Inventory Management: Tracking stock levels, managing inventory transactions like goods receipt and issue.
- Vendor Valuation: Evaluating vendor performance and managing vendor relationships.
- Material Valuation: Pricing and valuation of materials in stock, accommodating different valuation methods.
- Material Requirement Planning (MRP): Automated planning tool to ensure material availability.
SAP MM Integration with Other SAP Modules
1. Finance (FI) and Controlling (CO)
- Accounts Payable: Integrates with FI for processing payments to suppliers.
- Cost Accounting: MM transactions are reflected in CO for accurate cost tracking and controlling.
- Budget Management: Ensures procurement aligns with financial budgets and planning.
2. Sales and Distribution (SD)
- Inventory Management: MM provides inventory data for sales order fulfillment.
- Pricing: Material costs from MM influence pricing decisions in SD.
- Delivery and Shipping: MM coordinates with SD for the availability of products for customer orders.
3. Production Planning (PP)
- Material Requirements: MM feeds material availability data to PP for production scheduling.
- Bill of Materials (BOM): MM manages the BOM, essential for production planning.
- Procurement for Production: MM ensures materials needed for production are procured timely.
4. Plant Maintenance (PM)
- Spare Parts Management: MM manages inventory of spare parts required for maintenance.
- Procurement of Services: MM handles the procurement of external services for maintenance activities.
5. Quality Management (QM)
- Material Inspection: Integration with QM for quality inspection during the goods receipt process.
- Vendor Evaluation: QM feedback influences vendor evaluation in MM.
6. Human Resources (HR)
- Purchase of HR Services: Procurement of training, recruitment services, etc.
- Expense Management: Integration with travel and expense management in HR.
7. Project Systems (PS)
- Project Material Procurement: MM manages procurement for project-specific materials.
- Budgeting and Cost Management: Material costs are integrated into project budgeting in PS.
8. Supplier Relationship Management (SRM)
- Vendor Collaboration: Enhanced supplier collaboration for procurement processes.
- Contract Management: MM leverages contracts managed in SRM.
9. Supply Chain Management (SCM)
- Supply Planning: MM’s inventory data assists in overall supply planning.
- Demand Forecasting: Information from MM contributes to accurate demand forecasting in SCM.
Procurement to Pay (P2P) cycle in SAP MM
The Procure-to-Pay (P2P) cycle in SAP Material Management (MM) is a fundamental process that outlines the complete flow of purchasing activities from the identification of a requirement to the payment of the invoice. It’s a critical component of supply chain management, ensuring efficient procurement operations.
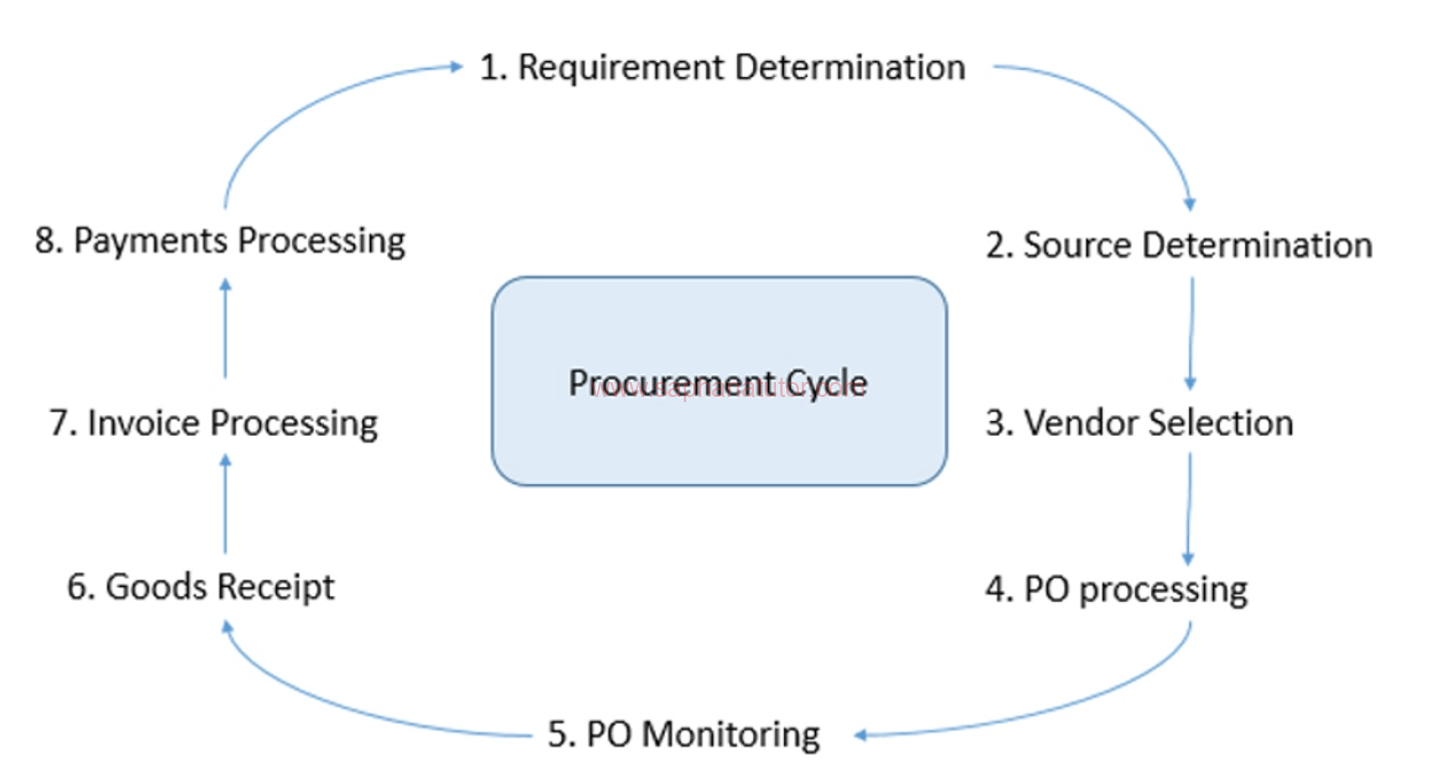
SAP MM Course Curriculum: Tutorial Series
Tutorial 1: Introduction to SAP and Material Management
- SAP Overview
- Basics of SAP R/3 and Business Framework Architecture.
- SAP MM Overview
- Organizational Structure in an Enterprise.
- Key Processes: Procurement, Purchase Order, Goods Receipt, Invoice Verification, Purchase Requisition.
Tutorial 2: Procurement Process in SAP MM
- Role of MM in Procurement.
- Procuring materials and services, identifying supply sources, and managing vendor relations.
- Material Master Data.
- In-depth look at Materials Master and Vendor Master.
Tutorial 3: Purchasing Essentials in SAP MM
- Purchasing Operations
- Detailed exploration of Purchase Info Record, Purchase Orders (PO), Purchase Requisitions (PR), and Request for Quotations (RFQ).
- Special Stocks and Procurement Types.
- Managing different types of stocks and orders, including services and subcontracting.
- Source Determination.
- Techniques for effective source finding and selection.
Tutorial 4: Advanced Purchasing Techniques
- Release Procedures for Purchasing Documents.
- Comprehensive understanding of characteristics, class, release groups, codes, and strategies.
- Inventory Management.
- Managing inventory with a focus on movement types, goods receipt, issue, transfer posting, and more.
Tutorial 5: Invoicing and Valuation in SAP MM
- Logistics Invoice Verification.
- Process of verifying and posting incoming invoices.
- Valuation and Account Assignment.
- Techniques for materials valuation and linking MM with Financial Accounting.
Tutorial 6: Material Requirements Planning (MRP)
- Principles of MRP.
- Understanding stock monitoring and procurement proposals based on consumption.
- MRP Procedures and Planning.
- Detailed insights into planning requirements and overall procedures.
Tutorial 7: Reporting and Configuration in SAP MM
- Reporting Techniques.
- Leveraging SAP MM for document-level reporting and Logistics Information System.
- MM Configuration.
- Setting up and configuring the enterprise structure, including organizational levels.
Tutorial 8: Integrating MM with Various SAP Modules
- Materials Master Fundamentals.
- Detailed exploration of material types, groups, storage conditions.
- Integration Overview
- How SAP MM integrates with SAP FICO, SAP SD, and PP modules.
MM’s integration with other SAP modules is fundamental for the seamless functioning of an enterprise’s operations. This integration ensures that material management processes are aligned with financial controls, sales processes, production planning, and overall business strategy. Effective use of MM can significantly contribute to optimizing costs, improving operational efficiency, and ensuring timely availability of materials.
Conclusion
This curriculum offers a structured and comprehensive approach to learning SAP MM, designed to provide deep insights into each aspect of Material Management within SAP. Each tutorial is crafted to build upon the last, ensuring a thorough understanding of SAP MM’s capabilities and integrations.